Der Motor muss vor der Demontage gründlich von Schmutz befreit werden
Es wird empfohlen, den Motor auf einem Ständer zu zerlegen und wieder zusammenzubauen, der es ermöglicht, den Motor an Positionen zu installieren, die bei der Demontage und Montage einen einfachen Zugang zu allen Teilen ermöglichen.
Die Demontage und Montage von Motoren muss mit Werkzeugen entsprechender Größe (Schraubenschlüssel, Abzieher, Vorrichtungen) erfolgen, deren Arbeitsfläche in gutem Zustand sein muss.
Bei einer individuellen Reparaturmethode müssen für weitere Arbeiten geeignete Teile an ihren ursprünglichen Plätzen eingebaut werden.
Dazu müssen Teile wie Kolben, Kolbenbolzen, Kolbenringe, Pleuel, Laufbuchsen, Ventile, hydraulische Stößel usw. beim Ausbau aus dem Motor so gekennzeichnet werden, dass sie nicht beschädigt werden Teilen (Stanzen, Beschriften, Anbringen von Schildern usw.) oder platzieren Sie sie in der Reihenfolge, die ihrer Position am Motor entspricht, auf Gestellen mit nummerierten Fächern.
Wenn Sie die unpersönliche Methode der Motorreparatur anwenden, müssen Sie bedenken, dass die Pleueldeckel mit Pleuelstangen, die Hauptlagerdeckel mit dem Zylinderblock, die Nockenwellenstützdeckel mit dem Zylinderkopf als Baugruppe verarbeitet werden und daher nicht verarbeitet werden können zerlegt.
Kurbelwelle, Schwungrad und Kupplung werden werkseitig separat ausgewuchtet und sind daher austauschbar.
Das Kupplungsgehäuse wird getrennt vom Zylinderblock verarbeitet und ist ebenfalls austauschbar. Bei hydraulischen Spannern ist die Demontage des Gehäuses mit dem Kolben nicht zulässig.
Es wird empfohlen, den Motor in der folgenden Reihenfolge zu zerlegen:
- - Entfernen Sie die Kupplungsausrückgabel;
- - Entfernen Sie das Getriebe vom Motor;
- - Entfernen Sie den Lüfter; - Kupplungsgehäuse und Anlasser entfernen;
- - Installieren Sie den Motor zur Demontage auf einem Ständer;
- - Lösen Sie die Schrauben, mit denen die Kühlmittelriemenscheibe befestigt ist;
- - Lösen Sie die Schraube, mit der die Spannrolle befestigt ist;
- - Lösen Sie die Riemenspannung, indem Sie die bewegliche Schraube der Spannrolle lösen, und entfernen Sie den Riemen;
- - Lösen Sie die Schrauben, mit denen die Riemenscheibe der Kühlmittelpumpe befestigt ist, entfernen Sie die Riemenscheibe und den Riemenscheibenreflektor;
- - Entfernen Sie die Kabel mit Spitzen von den Zündkerzen, schrauben Sie die Zündkerzen ab;
- - Trennen Sie die Hochspannungskabel von den Zündspulenanschlüssen und entfernen Sie die mit den Spitzen bestückten Kabel;
- - Schrauben Sie die Überwurfmuttern von den Anschlüssen des Ansaugrohrs und des Abgaskrümmers ab und entfernen Sie das Rückführungsrohr;
- - Schrauben Sie die Ventildeckelschrauben ab und entfernen Sie die Ventildeckelbaugruppe mit Zündspulen, Schrauben, Halterungen und Unterlegscheiben;
- - Entfernen Sie die Kraftstoffleitung von der Kraftstoffpumpe zum Kraftstofffeinfilter;
- - Entfernen Sie die Kraftstoffpumpe;
- - Entfernen Sie die vordere Zylinderkopfabdeckung;
- - Entfernen Sie die oberen und mittleren Kettenführungen;
- - Entfernen Sie die Abdeckung mit der Dichtung des oberen hydraulischen Kettenspanners;
- - Entfernen Sie den hydraulischen Spanner;
- - Lösen Sie die Schraube, mit der das Einlassnockenwellenrad befestigt ist, und entfernen Sie den Exzenter und das Kettenrad;
- - Entfernen Sie die Antriebskette von den Nockenwellenrädern;
- - Entfernen Sie das Kettenrad von der Auslassnockenwelle;
- - Lösen Sie die Befestigungsschrauben der Nockenwellenabdeckungen, entfernen Sie die Abdeckungen und Druckflansche;
- - Entfernen Sie die Nockenwellen;
- - Entfernen Sie die hydraulischen Drücker mit einem Saugnapf oder Magneten und ordnen Sie sie in der Reihenfolge der Zylindernummerierung an;
- - Lösen Sie die Schrauben der Klemmen des Ansaugtrakt-Heizschlauchs und entfernen Sie die Schläuche von den Anschlüssen;
- - Lösen Sie die Klemmschraube der oberen Halterung des Generators;
- - Lösen Sie die Mutter der Schraube, mit der der Generator an der oberen Halterung befestigt ist, und entfernen Sie die Schraube und die Buchse. - Lösen Sie die Mutter der Schraube, mit der der Generator an der unteren Halterung befestigt ist, und entfernen Sie den Generator;
- - Entfernen Sie die Schläuche des Rückführungssystems von den Vergaseranschlüssen, dem thermischen Vakuumschalter und dem Rückführungsventil;
- - Lösen Sie die Schraube der Kraftstoffleitungsklemme am Vergaseranschluss und entfernen Sie den Schlauch vom Anschluss.
- - Schrauben Sie die Befestigungsmuttern des Vergasers ab, entfernen Sie Unterlegscheiben, Vergaser, Dichtungen und Distanzstücke;
- - Lösen Sie die Muttern, mit denen das Rückführungsventil befestigt ist, und entfernen Sie die Unterlegscheiben, das Ventil und die Dichtung;
- - Lösen Sie die Schraube, mit der der Feinkraftstofffilter befestigt ist, und entfernen Sie die Filterbaugruppe mit den Kraftstoffleitungen;
- - Schrauben Sie den thermischen Vakuumschalter ab;
- - Lösen Sie die Muttern, mit denen das Ansaugrohr befestigt ist, und entfernen Sie die Ansaugrohr-Unterlegscheiben und die Dichtung;
- - Schrauben Sie die Befestigungsmuttern des Auspuffkrümmers ab, entfernen Sie Unterlegscheiben, Auspuffkrümmer und Dichtungen;
- - Lösen Sie die Schlauchklemmen des Thermostatgehäuses;
- - Lösen Sie die Schrauben, mit denen das Thermostatgehäuse befestigt ist, und entfernen Sie das Gehäuse und die Dichtung;
- - Schrauben Sie den Anschluss des Öldrucksensors ab;
- - Lösen Sie die Zylinderkopf-Befestigungsschrauben, entfernen Sie die Schrauben und Unterlegscheiben; - Zylinderkopf entfernen;
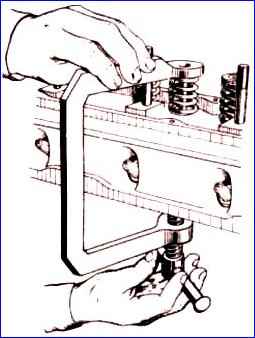
- - Demontieren Sie die Ventilfedern mit dem Werkzeug. Damit sich die Ventilfederplatte von den Crackern löst, müssen Sie nach dem Zusammendrücken der Federn mit dem Stiel eines Hammers leicht auf die Geräteplatte schlagen;
- - Entfernen Sie die Ventile und ordnen Sie sie in der Reihenfolge der Zylindernummerierung an;
- - Entfernen Sie die Öldichtungen mit einem Abzieher von den Führungsbuchsen. Es wird empfohlen, die Ventile bei Reparaturen am Zylinderkopf zu entfernen;
- - Drehen Sie den Motor um, wobei die Ölwanne nach oben zeigt. - Lösen Sie die Schrauben, mit denen das Kupplungsgehäuse des Verstärkers am Block befestigt ist, entfernen Sie die Unterlegscheiben und den Verstärker;
- - Lösen Sie die Schrauben und Muttern, mit denen die Ölwanne befestigt ist, entfernen Sie Unterlegscheiben, Ölwanne und Dichtung;
- - Lösen Sie die Befestigungsschraube des Ölpumpenhalters an der dritten Hauptlagerabdeckung;
- - Lösen Sie die Befestigungsschrauben der Ölpumpe, entfernen Sie die Ölpumpe, die Dichtung und die Sechskantwelle des Ölpumpenantriebs;
- - Lösen Sie die Klemmschraube der Kurbelwelle, entfernen Sie die Schraube und die Federscheibe;
- - Verwenden Sie ein Werkzeug, um die Kurbelwellenriemenscheibe zu entfernen;
- - Lösen Sie die Schrauben, mit denen die Kühlmittelpumpe an der Kettenabdeckung befestigt ist, entfernen Sie die Schrauben mit Unterlegscheiben, die Kühlmittelpumpe und die Dichtung;
- - Lösen Sie die Schraube, mit der die Spannrolle befestigt ist, und entfernen Sie die Spannrolle;
- - Entfernen Sie die Abdeckung und die Dichtung des hydraulischen Spanners der ersten Stufe und entfernen Sie den hydraulischen Spanner;
- - Lösen Sie die Schraube, mit der der Synchronisationssensor befestigt ist, und entfernen Sie den Sensor;
- - Lösen Sie die Schrauben, mit denen die Kettenabdeckung befestigt ist, entfernen Sie die Abdeckung und die untere Generatorhalterung;
- - Entfernen Sie die Kette der zweiten Stufe des Nockenwellenantriebs vom Antriebsritzel der Zwischenwelle;
- - Lösen Sie die Schrauben, mit denen die Zwischenwellenkettenräder befestigt sind, und entfernen Sie die Kettenräder und die Kette;
- - Lösen Sie die Schrauben, mit denen der Zwischenwellenflansch befestigt ist, und entfernen Sie die Schrauben mit Unterlegscheiben und dem Flansch;
- - Lösen Sie die Schrauben, mit denen die Abdeckung des Ölpumpenantriebs befestigt ist, und entfernen Sie die Abdeckung und die Dichtung;
- - Schrauben Sie die Mutter des Ölpumpen-Antriebszahnrads ab und entfernen Sie die Zahnradbaugruppe mit der Mutter;
- - Entfernen Sie die Zwischenwelle;
- - Drücken Sie die Passfeder aus der Zwischenwelle;
- - Entfernen Sie die Buchse und das Kettenrad mit einem Abzieher von der Kurbelwelle;
- - Lösen Sie die Schraube, mit der der Kettenspannerschuh der ersten Stufe des Nockenwellenantriebs befestigt ist, und entfernen Sie den Schuh;
- - Lösen Sie die Schraube, mit der der Kettenspannerschuh der zweiten Stufe des Nockenwellenantriebs befestigt ist, und entfernen Sie den Schuh;
- – Schrauben Sie die Schuhbolzenverlängerung ab und entfernen Sie die Verlängerung;
- - Lösen Sie die Schrauben, mit denen die untere Kettenführung befestigt ist, und entfernen Sie die Führung;
- - Lösen Sie die Muttern, mit denen die Abdeckungen der ersten und vierten Pleuelstangen befestigt sind, entfernen Sie die Pleuelstangenabdeckungen mit Laufbuchsen, entfernen Sie die Laufbuchsen von den Betten der Pleuelstangenabdeckungen;
- - Entfernen Sie die Kolben- und Pleuelstangenbaugruppen vom ersten und vierten Zylinder;
- - Installieren Sie die Kurbelwelle so, dass sich der zweite und dritte Pleuelzapfen in der oberen Position befinden, lösen Sie die Muttern, mit denen die Abdeckungen des zweiten und dritten Pleuels befestigt sind, entfernen Sie die Pleuelkappen mit Laufbuchsen, entfernen Sie die Laufbuchsen von den Betten der Pleueldeckel;
- - Entfernen Sie die Kolben mit Pleuelstangen vom zweiten und dritten Zylinder;
- - Setzen Sie einen genuteten Dorn in die Verzahnung der angetriebenen Scheibe ein;
- - Lösen Sie nacheinander in mehreren Schritten die Schrauben, mit denen die Kupplungsdruckplatte befestigt ist, und entfernen Sie die Scheibe;
- - Entfernen Sie die angetriebene Kupplungsscheibe mit dem Keildorn;
- - Lösen Sie die Befestigungsschrauben des Schwungrads und entfernen Sie das Schwungrad vom Stift;
- - Lösen Sie die Schrauben, mit denen die hintere Abdeckung befestigt ist, und entfernen Sie die mit der Gummimanschette zusammengebaute hintere Abdeckung;
- - Lösen Sie die Schrauben, mit denen die Hauptlagerdeckel befestigt sind, und entfernen Sie die Schrauben;
- - Entfernen Sie die Hauptlagerdeckel mit einem Abzieher und die oberen Halbscheiben des Kurbelwellen-Axiallagers;
- - Entfernen Sie die Kurbelwelle und die unteren Halbscheiben des Kurbelwellen-Drucklagers.
- - Entfernen Sie die Hauptlager von den Zylinderblockbetten und von den Hauptlagerdeckeln;
- - Installieren Sie die Hauptlagerdeckel entsprechend der Nummerierung im Block;
- - Befestigen Sie die Hauptlagerdeckel mit Schrauben;
- - Schrauben Sie die Mutter ab, mit der der Klopfsensor befestigt ist, entfernen Sie die Unterlegscheibe und den Sensor;
- - Schrauben Sie den Ölfilter ab;
- - Schrauben Sie den Ablasshahn vom Zylinderblock ab; - Pleuellager von den Pleueln entfernen; - Pleuelkappen auf die Befestigungsbolzen montieren, Muttern eindrehen;
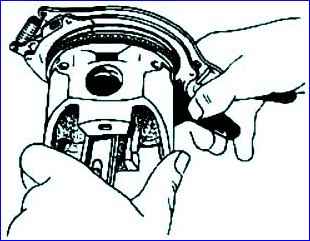
- Entfernen Sie die Kompressionsölringe mit einem Abzieher von den Kolben. - Entfernen Sie die Sicherungsringe;
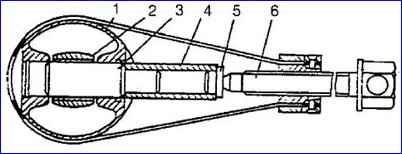
- Drücken Sie die Kolbenbolzen mit einer Vorrichtung und einem Dorn aus den Kolben heraus
Reparatur von Teilen, Komponenten, Baugruppen und Motorsystemen
Zylinderblock, Kolben, Pleuel, Zwischenwelle
Ein Zylinderblock mit Löchern in den Zylinderwänden, dem Wassermantel und dem Kurbelgehäuse oder mit Rissen in der oberen Ebene und Rippen, die die Hauptlager tragen, muss ersetzt werden.
Durch den Verschleiß nehmen die Zylinder des Blocks die Form eines unregelmäßigen Kegels in der Länge und eines Ovals im Umfang an.
Der Verschleiß erreicht seinen größten Wert im oberen Teil der Zylinder im Bereich des oberen Kompressionsrings, wenn sich der Kolben im oberen Totpunkt befindet; die kleinste – im unteren Teil, mit der Kolbenposition am BDC.
Bei der Reparatur von Zylindern stehen zwei Reparaturgrößen zur Verfügung: 1. und 2. Größe. Kolben und Kolbenringe werden mit den gleichen Reparaturmaßen gefertigt.
Alle Zylinder des Blocks müssen in der Regel auf das gleiche Reparaturmaß mit mm-Abweichungen bearbeitet werden, die für Zylinder mit Nenngröße gelten, mit Ausnahme der Fälle, in denen flache Kratzer auf dem Zylinderspiegel „entfernt“ werden müssen (im Rahmen einer Vergrößerung des Zylinderdurchmessers um 0,10 mm) - in diesem Fall können nur defekte Zylinder korrigiert werden.
Wenn nur eine begrenzte Anzahl von Kolben repariert werden muss, wird empfohlen, die Durchmesserabweichungen für jeden Zylinder zu berechnen (basierend auf der tatsächlichen Größe des Kolbenmanteldurchmessers, der für den Betrieb in einem bestimmten Zylinder mit einem Spiel von 0,036–0,060 vorgesehen ist). mm) und bohren Sie die Zylinder auf diese Maße.
Zylinderformabweichungen müssen innerhalb des Toleranzbereichs der Maßgruppe für den Zylinderdurchmesser liegen.
Die Reparatur von Zwischenwellen-Stützbuchsen besteht darin, sie durch Reparaturbuchsen (mit erhöhter Dicke) zu ersetzen und anschließend auf das Nenn- oder Reparaturmaß mit der für Stützen des Nennmaßes festgelegten Toleranz aufzubohren – abhängig vom Grad der Abnutzung der Welle Lagerzapfen.
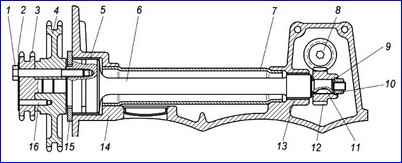
Zwischenwelle: 1 – Bolzen; 2 – Sicherungsblech; 3 – Antriebskettenrad; 4 – angetriebenes Kettenrad; 5 – vordere Wellenbuchse; 6 – Zwischenwelle; 7 – Rohr; 8 – angetriebenes Zahnrad des Ölpumpenantriebs; 9 – Ring; 10 – Nuss; 11 – Schlüssel; 12 – Antriebsrad des Ölpumpenantriebs; 13 – hintere Wellenbuchse; 14 – Zylinderblock; 15 – Zwischenwellenflansch; 16 - Stift
Vor der Reparatur der Stützen ist es notwendig, Rohr 7 zu entfernen
Beim Einbau von Reparaturbuchsen ist darauf zu achten, dass die Löcher in den Ölkanälen übereinstimmen. Das Aufbohren der Zwischenwellenträger erfolgt in einem Arbeitsgang, um die Ausrichtung sicherzustellen.
Für den Fall, dass der Verschleiß den maximal zulässigen Wert überschreitet, werden die Zwischenwellenzapfen auf ein Reparaturmaß mit der Toleranz geschliffen, die für Zapfen mit Nenngröße festgelegt ist.
Beschädigungen an Gewindelöchern in Form von Kerben oder Gewindebrüchen von weniger als zwei Gewindegängen werden mit einem Gewindebohrer auf Nennmaß wiederhergestellt.
Gewindelöcher mit verschlissenen oder gebrochenen Gewindegängen von mehr als zwei Gewindegängen werden durch das Schneiden vergrößerter Gewinde, den Einbau von Gewindeschrauben und das anschließende Einschneiden von Gewinden einer Nenngröße oder den Einbau von Gewindespiraleinsätzen wiederhergestellt. Die letzte Methode ist die effektivste und weniger arbeitsintensiv.
Kurbelwelle
Bei Rissen muss die Kurbelwelle ausgetauscht werden.
Um Verschleißrückstände in den Hohlräumen der Pleuellagerzapfen und in den Ölkanälen der Kurbelwelle zu entfernen, ist es notwendig, die Stopfen der Lagerzapfen abzuschrauben, sie auszuglühen (mit einer auf 80° C erhitzten Natronlauge) und Reinigen Sie die Hohlräume und Kanäle mit einer Metallbürste.
Nach der Reinigung müssen sie mit Kerosin gewaschen, ausgeblasen und mit Druckluft getrocknet werden. Anschließend müssen die Stopfen mit einem Drehmoment von 38–42 Nm (3,8–4,2 kgf·m) festgezogen werden.
Wenn das Gewinde in Löchern mit bis zu zwei Gewindegängen beschädigt ist, wird es mit einem Gewindebohrer auf die Nenngröße wiederhergestellt. Bei einem Bruch von zwei oder mehr Gewinden erfolgt die Reparatur wie folgt:
- - Gewinde in die Löcher für die Schwungrad-Befestigungsschrauben – durch Einbau von Gewindespiraleinsätzen;
- - Gewinde in das Loch für die Ratsche – durch Schneiden eines Reparaturgewindes; - Gewinde in Löcher für Stopfen - durch Schneiden von Reparaturgewinden.
Pleuel- und Hauptlagerzapfen, die innerhalb der Reparaturgröße abgenutzt sind, werden auf die nächstgelegene Reparaturgröße (1., 2. oder 3.) geschliffen, wobei die für Lagerzapfen der Nenngröße festgelegte Toleranz gilt (alle Lagerzapfen werden auf die gleiche Reparaturgröße geschliffen).
Die scharfen Kanten der Fasen der Ölkanäle werden mit einem konischen Schleifwerkzeug abgestumpft und anschließend werden die Lagerzapfen poliert.
Zylinderkopf, Ventiltrieb und Nockenwellen
Bei Löchern, Ausbrüchen und Rissen an den Wänden der Brennkammern sowie bei Zerstörung der Brücken zwischen den Ventilsitzbuchsen muss der Zylinderkopf durch einen neuen ersetzt werden.
Die Reparatur von Gewindelöchern erfolgt auf die gleiche Weise wie für die Gewindelöcher des Zylinderblocks.
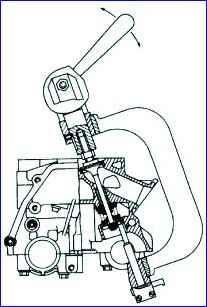
Um die Dichtheit der Ventile zu überprüfen, ist es notwendig, abwechselnd Kerosin in die Einlass- und Auslasskanäle des Zylinderkopfes zu gießen.
Das Austreten von Kerosin unter den Ventilplatten weist auf deren Undichtigkeit hin.
Undichte Ventile werden mit einem Ventilfederspanner aus dem Zylinderkopf entfernt.
Platzieren Sie die Ventile bei der Demontage in der Reihenfolge, in der sie sich im Kopf befinden, damit sie später an ihren ursprünglichen Stellen eingebaut werden können.
Vor dem Läppen des Ventils sollten Sie prüfen, ob sich die Ventilplatte verzieht und ob Ventil und Sitz durchgebrannt sind.
Liegen diese Mängel vor, ist eine Wiederherstellung der Dichtheit des Ventils durch Einschleifen nicht möglich und es muss zunächst der Sitz aufgebohrt und das beschädigte Ventil durch ein neues ersetzt werden.
Wenn der Spalt zwischen Ventilschaft und Führungsbuchse 0,20 mm überschreitet, sollten Ventil und Buchse durch neue ersetzt werden.
Für Ersatzteile werden Ventile in Nenngrößen und Führungsbuchsen mit einer Bearbeitungszugabe entlang des Innendurchmessers nach dem Einpressen in den Kopf und mit einem Außendurchmesser von drei Reparaturgrößen hergestellt: die erste – mit einer Vergrößerung von 0,02 mm vom Nennwert, der zweite – mit einer Erhöhung um 0,2 mm vom Nennwert, der dritte – mit einer Erhöhung von 0,02 mm vom zweiten Reparaturmaß.
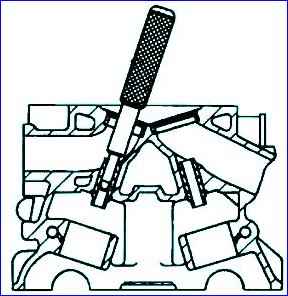
Das Auspressen einer verschlissenen Führungsbuchse erfolgt mit einem Dorn. Vor dem Auspressen der Führungsbuchsen muss die Wartbarkeit des Zylinderkopfes ermittelt werden.
Der Zylinderkopf ist reparierbar, wenn nach der Bearbeitung des Ventilsitzes der Abstand von der Nockenwellenachse bis zum Ende des Ventilschafts, der gegen die Arbeitsfase des Sitzes gedrückt wird, mindestens 35,5 mm beträgt.
Wenn diese Bedingung nicht erfüllt ist, kann der Zylinderkopf nicht repariert werden. Der Zylinderkopf kann auch nicht repariert werden, wenn die Oberfläche neben dem Block eine Unebenheit von mehr als 0,1 mm aufweist.
Beim Einbau neuer Führungsbuchsen müssen diese in Kohlendioxid („Trockeneis“) auf eine Temperatur von minus 40–45 °C abgekühlt und der Zylinderkopf auf eine Temperatur von plus 160–175 °C erwärmt werden .
Bei der Montage sollten die Buchsen frei oder mit leichtem Kraftaufwand in das Kopfloch eingeführt werden.
Buchsen der ersten Reparaturgröße werden ohne zusätzliche Bearbeitung der Löcher im Kopf in den Kopf eingebaut, Buchsen der zweiten und dritten Reparaturgröße werden mit Vorbohren (Reiben) der Löcher auf einen Durchmesser von 14,2 mm eingebaut.
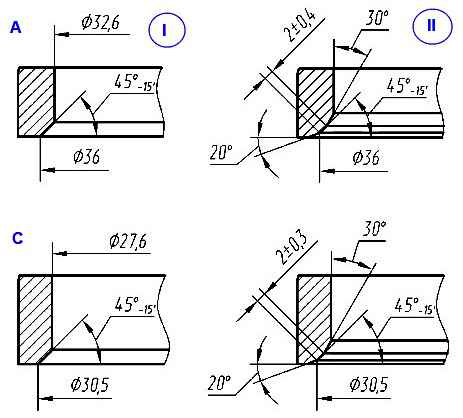
Ventilsitze schleifen: A – Einlassventilsitz; C – Auslassventilsitz; I – neuer Sattel; II – Sattel nach der Reparatur
Bearbeiten Sie nach dem Einbau und Reiben der Buchsen die Sitzfasen (durch Schleifen oder Bohren) und zentrieren Sie das Werkzeug entlang des Lochs in der Buchse.
Bei der Verarbeitung sollten Sie die in Abb. 7 angegebenen Maße einhalten und darauf achten, dass die Fase am Ventilsitz konzentrisch zum Loch in der Buchse ist (der Rundlauf der Arbeitsfase des Sitzes relativ zum Buchsenloch ist zulässig). nicht mehr als 0,05 mm).
Nach der Bearbeitung der Fasen muss deren Breite reduziert werden, indem die Innenfläche der Sitze in einem Winkel von 30° auf eine Größe von (2±0,4) mm für die Einlassventilsitze (2±0,3) bearbeitet wird ) mm für die Auslassventilsitze.
Anschließend schleifen Sie die Ventile mit einer Läpppaste, die aus einem Teil M-20-Mikropulver und zwei Teilen I-20A-Öl besteht.
Vor dem Zusammenbau des Zylinderkopfes ist es notwendig, die Brennkammern sowie die Einlass- und Auslasskanäle von Kohlenstoffablagerungen und -ablagerungen zu reinigen. Nach dem Benetzen der Kohlenstoffablagerungen mit Kerosin wird das Verspritzen von Kohlenstoffablagerungen beim Entfernen verhindert und das Eindringen verhindert von giftigem Staub beim Einatmen.
Wischen Sie sie ab und blasen Sie sie mit Druckluft aus. Bei den eingebauten Ventilführungen ist es notwendig, gleichzeitig die Federstützscheiben mit einem Dorn zu montieren und die Wellendichtringe aufzudrücken.
Ventilschäfte mit Motoröl schmieren, Ventile entsprechend der Einbaureihenfolge in die Buchsen einsetzen und mit einem Werkzeug mit den Federn zusammenbauen.
Stellen Sie sicher, dass die Cracker in die Ringnuten der Ventile passen. Kerosin hineingießen Einlass- und Auslasskanäle und stellen Sie sicher, dass die Ventile dicht sind. Um das Spiel in den Nockenwellenlagern zu ermitteln, müssen Sie alle Lagerdeckel entsprechend ihrer Nummern montieren.
Vor dem Einbau der Zylinderkopfhauben „1“, „2“, „3“, „4“, „5“, „6“, „7“ und „8“ müssen diese mit Motoröl geschmiert werden.
Die Zentrierung dieser Abdeckungen erfolgt mithilfe eines zylindrischen Dorns mit einem Durchmesser von 35–0,02 mm, der in einem Bett liegt.
Nachdem Sie die Abdeckungen mit einem Drehmoment von 19–23 Nm (1,9–2,3 kgf·m) festgezogen haben, entfernen Sie den Dorn zum hinteren Ende des Zylinderkopfs (in diesem Fall muss die hintere Abdeckung des Zylinderkopfs entfernt werden).
Wenn der Spalt in einem der Lager mehr als 0,15 mm beträgt, müssen Sie entweder den Zylinderkopf oder die Nockenwelle austauschen.
Der Spalt im Loch für den hydraulischen Drücker und den hydraulischen Drücker sollte 0,15 mm nicht überschreiten. Ist der Spalt größer, muss entweder der Hydrostößel oder der Zylinderkopf ausgetauscht werden.
Die Oberflächen der Lagerzapfen und Nocken müssen frei von Graten und tiefen Löchern sein und dürfen keinen über das maximal zulässige Maß hinausgehenden Verschleiß aufweisen.
Nach der Überprüfung der Wellen ist es notwendig, die Oberflächen der Zapfen und Nocken zu reinigen und zu polieren.
Hydraulischer Spanner Bei der Reparatur eines Motors müssen hydraulische Spanner zerlegt, ihre Teile gewaschen und wieder zusammengebaut („aufgeladen“) werden.
Die Demontage des hydraulischen Spanners erfolgt in der folgenden Reihenfolge:
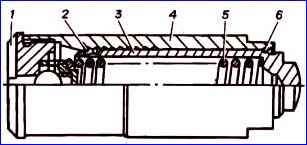
- - Ventilkörper 1 vom hydraulischen Spannerkörper 4 abschrauben; — Feder 5 und Stößel 3 aus Gehäuse 4 entfernen.
- Der hydraulische Spanner wird in der folgenden Reihenfolge zusammengebaut:
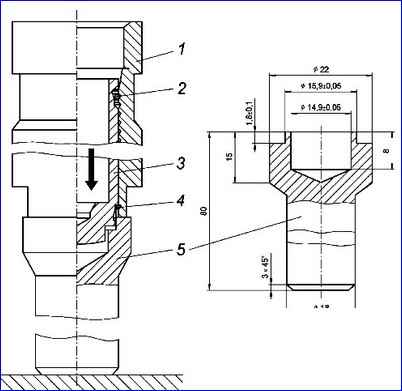
„Aufladen“ des hydraulischen Spanners mit einem Dorn: 1 - Gehäuse; 2 – Sicherungsring; 3 - Kolben; 4 - Sicherungsring; 5 - Dorn
- - Installieren Sie das hydraulische Spanngehäuse 1 auf dem vertikal befestigten Dorn 5;
- - Setzen Sie den Kolben 3 in das Gehäuse des hydraulischen Spanners ein, bis der Sicherungsring 4 am Kolben im Dornriemen stoppt;
- - Drücken Sie einen Metallstab mit einem Durchmesser von 5–7 mm (Sie können einen Schraubenzieher verwenden) auf die Unterseite des Kolbens oder mit Ihrem Finger auf das Ende des Kolbens, sodass der Sicherungsring aus der Nut am Kolben herausragt bewegt sich in die Nut des Gehäuses (ein leichtes Einrasten ist zu hören). Der Körper und der Kolben werden fixiert – „Laden“. Gleichzeitig gelangt der Sicherungsring 2 in die erste Nut des Gehäuses;
- - Füllen Sie den inneren Hohlraum des Gehäuses und des Kolbens mit sauberem Motoröl, das für den Motor verwendet wird;
- - Setzen Sie eine Feder in den Kolben ein;
- - Installieren Sie das hydraulische Spannventil an der Feder, drücken Sie die Feder zusammen, ziehen Sie es fest und schrauben Sie es dann manuell in das Gehäuse, während der Sicherungsring am Kolben in der Nut des Gehäuses liegen und den Kolben daran hindern sollte sich im Körper bewegen;
- - Entfernen Sie den hydraulischen Spanner vom Dorn und schrauben Sie schließlich das Ventil mit einem Drehmoment von 19–24 N·m (1,9–2,4 kgf·m) in das Gehäuse ein. Verwenden Sie dazu eine 1,8–1,9 mm dicke Platte, die in einen Schraubstock eingespannt ist. und einen Schlüssel „19“, wie bei der Demontage des hydraulischen Spanners.
Kühlmittelpumpe
Die Demontage und Montage der Pumpe erfolgt ähnlich wie bei den Motoren ZMZ-4025, -4026.
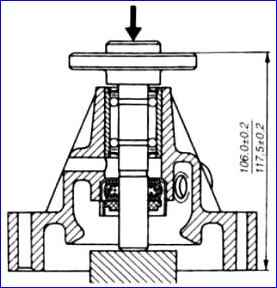
Der einzige Unterschied besteht darin, dass beim Aufpressen auf die Lagerwelle der Nabe der Pumpenriemenscheibe die Größe bei (106 ± 0,2) mm gehalten werden sollte.
Ölpumpe Bei Störungen im Schmiersystem, die durch Störungen des Öls verursacht werden Pumpe, sie muss zerlegt werden.
Zur Demontage müssen Sie Folgendes tun: - Biegen Sie die Drähte des Gitterrahmens, entfernen Sie den Rahmen und das Gitter;
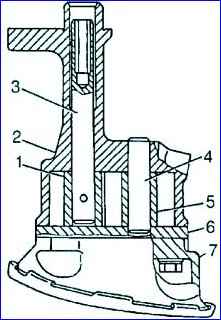
Ölpumpe: 1 - Antriebsrad; 2 - Körper; 3 - Walze; 4 - Achse; 5 – angetriebenes Zahnrad; 6 - Partition; 7 - Einlassrohr mit Netz und Druckminderventil
- - Lösen Sie die vier Schrauben, entfernen Sie das Ansaugrohr 7 und die Trennwand 6; — Entfernen Sie das angetriebene Zahnrad 5 und die Welle 3 mit dem montierten Antriebszahnrad 7 aus dem Gehäuse;
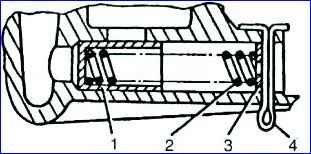
Reduzierventil: 1 - Kolben; 2 - Frühling; 3 - Unterlegscheibe; 4 - Splint
- - Entfernen Sie die Unterlegscheibe 3, die Feder 2 und den Kolben 7 des Druckminderventils vom Einlassrohr, nachdem Sie zuvor den Splint entfernt haben
Vorbereitende Arbeiten vor dem Zusammenbau der Motoren ZMZ-4061, ZMZ-4063 sind die gleichen wie vor dem Zusammenbau der Motoren ZMZ-4025, ZMZ-4026.
Der Zusammenbau des Motors muss in der folgenden Reihenfolge erfolgen:
- - Befestigen Sie den Zylinderblock am Ständer, prüfen Sie sorgfältig den Zylinderspiegel, entfernen Sie ggf. den nicht abgenutzten Riemen über dem oberen Kompressionsring mit einem Schaber.
Das Metall sollte bündig mit der abgenutzten Oberfläche des Zylinders entfernt werden;
- - Schrauben Sie die Ölkanalstopfen ab und blasen Sie alle Ölkanäle mit Druckluft aus, schrauben Sie die Stopfen fest;
Hinweis: Die Kurbelwelle, das Schwungrad und die Kupplungsbaugruppe sind nicht ausgewuchtet
- - Wischen Sie mit einer Serviette das Bett unter den Laufbuchsen im Block und in der Hauptlagerabdeckung ab; — Installieren Sie die oberen (mit Rillen) Hauptlagerschalen im Blockbett und die unteren (ohne Rillen) im Abdeckbett;
- - Wischen Sie die Laufbuchsen mit einer Serviette ab und schmieren Sie sie mit Motoröl;
- - Wischen Sie die Haupt- und Pleuelzapfen der Kurbelwelle mit einer Serviette ab, schmieren Sie sie mit sauberem Motoröl und bauen Sie die Welle in den Zylinderblock ein;
- - Mit Motoröl schmieren und die Halbscheiben des Drucklagers einbauen: die oberen – in den Nuten des dritten Hauptbetts des Zylinderblocks (mit der Gleitschicht zur Kurbelwellenwange hin); die unteren - zusammen mit der Abdeckung des dritten Hauptlagers. Die Antennen der Halbscheiben sollten in die Nuten der Abdeckung passen;
- - Bringen Sie die Abdeckungen der verbleibenden Stützen an den entsprechenden Hauptlagerzapfen an, schrauben Sie die Schrauben, mit denen die Hauptlagerabdeckungen befestigt sind, ein und ziehen Sie sie mit einem Drehmoment von 100–110 Nm (10–11 kgf·m) fest, nachdem Sie zuvor die Gewinde geschmiert haben die Schrauben mit Motoröl;
- - Drehen Sie die Kurbelwelle, ihre Drehung sollte mit geringem Kraftaufwand frei möglich sein;
- - Nehmen Sie den Deckel mit der Gummi-Öldichtung am hinteren Ende der Kurbelwelle und prüfen Sie die Eignung der Öldichtung für weitere Arbeiten. Wenn die Öldichtung abgenutzte Arbeitskanten aufweist oder den Kurbelwellenflansch nur schwach abdeckt, ersetzen Sie sie durch eine neue.
Es wird empfohlen, die Öldichtung mit einem Dorn in den Deckel zu drücken;
- - Füllen Sie 2/3 des Hohlraums zwischen der Arbeitskante und der Öldichtungsmanschette mit CIATIM-221-Schmiermittel, montieren Sie die Abdeckung und befestigen Sie sie mit Schrauben am Block mit einem Drehmoment von 12–18 Nm (1,2–1,8 kgf·m). ). Zentrieren Sie die Abdeckung mit einem Dorn;
- - Montieren Sie das Schwungrad am hinteren Ende der Kurbelwelle, sodass das Loch im Schwungrad mit dem Stift übereinstimmt;
- - Installieren Sie die Unterlegscheibe der Schwungradschrauben, befestigen Sie die Schrauben und ziehen Sie sie mit einem Drehmoment von 72–80 Nm (7,2–8,0 kgf·m) fest;
- - Eine Distanzhülse in das Schwungrad einbauen und das Kugellager 80203AC9 mit Schutzscheiben einpressen.
Führen Sie die Untermontage der Pleuel- und Kolbengruppe durch. Die Auswahl der Kolben für die Blockzylinder sowie der Kolbenbolzen für die Kolben und Pleuelstangen sollte bei einer Temperatur der Teile (20 ± 3)° C erfolgen.
Kolben nach Außendurchmesser und Zylinder nach Innendurchmesser werden in fünf Größengruppen sortiert.
Kolben derselben Größengruppe wie die Zylinder müssen in gebohrte oder neue Zylinder des Blocks eingebaut werden.
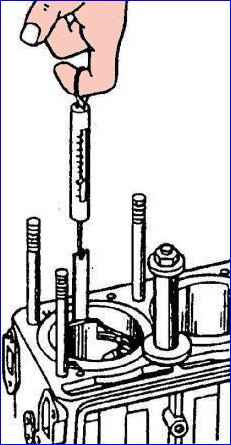
Eine Auswahl aus benachbarten Gruppen ist zulässig. In diesem Fall erfolgt die Auswahl wie bei der Auswahl von Kolben für Arbeitszylinder auf der Grundlage der Zugkraft eines Prüfbandes mit einer Dicke von 0,05 mm und einer Breite von 10 mm.
Das Fühlerband wird zwischen Zylinder und Kolben über die gesamte Höhe des Kolbens und in einer Ebene senkrecht zur Kolbenbolzenachse entlang des größten Durchmessers des Kolbens angebracht. Die Kraft auf das Dynamometer, das mit dem Sondenband verbunden ist, sollte 35–45 N (3,5–4,5 kgf) betragen.
Kolbenmarkierung – ein Buchstabe, der die Gruppe angibt, ist auf dem Kolbenboden eingeprägt;
- Die Reparaturvergrößerung wird durch die Aufschrift „406“ (Standardgröße) oder „406AR“ (Reparaturvergrößerung 0,5) oder „406BR“ (Reparaturvergrößerung 1,0) angezeigt, die auf der Seitenwand eines der Vorsprünge eingegossen ist den Kolbenbolzen.
Der Buchstabe, der die Zylindergruppe angibt, ist auf der Außenfläche des Blocks rechts gegenüber jedem Zylinder aufgemalt. Um die Auswahl zu erleichtern, sind Bolzen, Pleuel und Kolben in der Reihenfolge abnehmender Größe in vier Größengruppen unterteilt.
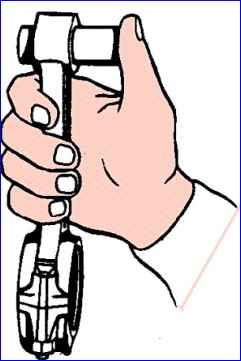
Markierung von Fingern und Pleuelstangen Die Finger und Pleuelstangen werden mit Farbe markiert: Der Finger befindet sich auf der Innenfläche, die Pleuelstange befindet sich auf der Kopfstange. Kolben – in römischen Ziffern (geprägt) auf der Unterseite oder Farbe auf dem Gewichtsansatz.
Der Kolbenbolzen ist mit einem Spiel von 0,0045 bis 0,0095 mm auf eine Pleuelstange derselben oder einer benachbarten Gruppe abgestimmt.
Bei der Auswahl sollte der Kolbenbolzen unter der Kraft des Daumens fest, aber ohne zu verklemmen, in das Loch im oberen Kopf der Pleuelstange passen. Der Kolbenbolzen sollte leicht mit Motoröl geschmiert werden.
Da die Längenausdehnung des Kolbenmaterials etwa doppelt so groß ist wie die des Bolzens, passt der Bolzen bei normaler Raumtemperatur mit Übermaß in die Bohrung der Kolbennaben.
Die Größengruppen von Kolben und Bolzen müssen übereinstimmen. Der Kolben komplett mit Kolbenbolzen, Kolbenringen und Pleuelstange muss gewichtskontrolliert sein. Der Gewichtsunterschied zwischen den Sätzen pro Motor sollte 10 g nicht überschreiten.
Nach dem Zusammenbau der Kolben und Kolbenbolzen muss mit dem Zusammenbau der Pleuel- und Kolbengruppe in der folgenden Reihenfolge fortgefahren werden:
- - Reinigen Sie die Kolbenköpfe und Nuten für Kolbenringe von Kohlenstoffablagerungen;
- - Drücken Sie den Kolbenbolzen mit einem Werkzeug in den Kolben und die Pleuelstange. Erhitzen Sie in diesem Fall den Kolben auf eine Temperatur von 60-80 °C (das Drücken eines Fingers in einen kalten Kolben kann zu einer Beschädigung der Oberfläche der Löcher in den Kolbennaben sowie zu einer Verformung des Kolbens selbst führen).
Pleuelstangen und Kolben müssen vor der Montage mit dem Kolbenbolzen wie folgt ausgerichtet werden:
- - der Pfeil auf der Unterseite des Kolbens (oder die Aufschrift „FRONT“ auf der Außenseite der Bolzennabe), die Leiste auf der Seitenfläche der Pleuelabdeckung und der Vorsprung am Kurbelkopf des Pleuel sollte in eine Richtung gerichtet sein;
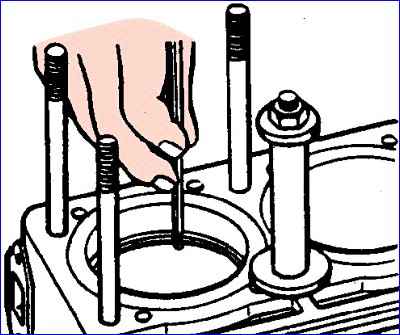
- - Kolbenringe für die Zylinder auswählen. Der thermische Spalt, gemessen in den Schlössern der im Zylinder platzierten Ringe, sollte 0,3–0,6 mm für Kompressionsringe und 0,5–1,0 mm für Stahlscheiben von Ölabstreifringen betragen.
Bei verschlissenen Zylindern sollte der kleinste Spalt 0,3 mm für Kompressionsringe und 0,5 mm für Stahlscheiben von Ölabstreifringen betragen;
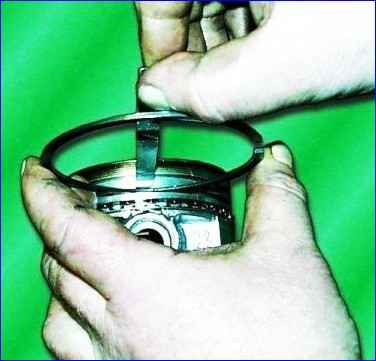
- - Überprüfen Sie den Spalt zwischen den Ringen und der Wand der Kolbennut mit einer Fühlerlehre. Überprüfen Sie den Umfang des Kolbens an mehreren Stellen.
Die Spaltgröße sollte im Bereich von 0,050–0,087 mm für den oberen und unteren Kompressionsring und 0,115–0,365 mm für den montierten Ölabstreifring liegen;
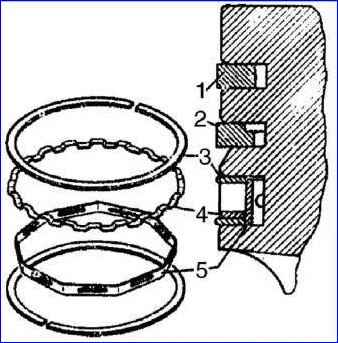
- - Setzen Sie die Kolbenringe mithilfe der Vorrichtung auf den Kolben. Platzieren Sie den unteren Kompressionsring mit der inneren Aussparung nach oben in Richtung der Unterseite des Kolbens. Die Ringe in den Nuten müssen frei beweglich sein;
- - Setzen Sie die Kolben wie folgt in die Zylinder ein:
- - Richten Sie die Pleuel-Kolben-Gruppe so aus, dass der Pfeil auf der Kolbenunterseite (oder die Aufschrift „FRONT“ auf der Nabe) nach vorne zeigt;
- - Wischen Sie die Pleuellager und deren Abdeckungen mit einer Serviette ab, wischen Sie die Buchsen ab und setzen Sie sie ein;
- - Drehen Sie die Kurbelwelle so, dass die Kurbeln des ersten und vierten Zylinders die Position einnehmen, die dem UT entspricht;
- - Schmieren Sie die Lager, den Kolben, den Pleuelzapfen und den ersten Zylinder mit sauberem Motoröl;
- - Bewegen Sie die Schlösser der Kompressionsringe in einem Winkel von 180° zueinander, die Schlösser der Ölabstreifringscheiben stehen ebenfalls in einem Winkel von 180° zueinander und 90° in Bezug auf die Schlösser der Kompressionsringe.
Fügen Sie die Verriegelung des Doppelfunktions-Expanders im 45°-Winkel zur Verriegelung einer der Ringscheiben ein;
- - Setzen Sie Sicherheitsmessingspitzen auf die Pleuelbolzen, drücken Sie die Ringe durch Crimpen zusammen oder verwenden Sie einen Dorn für den Einbau in den Kolbenzylinder;
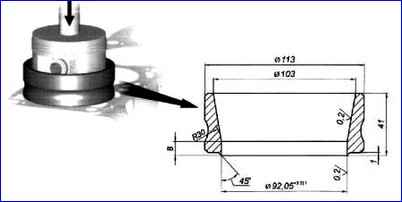
- - Setzen Sie den Kolben in den Zylinder ein. Vor dem Einbau des Kolbens sollten Sie noch einmal sicherstellen, dass die auf dem Pleuel und seinem Deckel eingestanzten Nummern mit der Seriennummer des Zylinders übereinstimmen, die korrekte Position des Kolbens und des Pleuels im Zylinder überprüfen;
- - Ziehen Sie die Pleuelstange am Kurbelkopf zum Pleuelzapfen, entfernen Sie die Messingspitzen von den Bolzen und setzen Sie die Pleuelstangenabdeckung auf. Der Pleueldeckel sollte so montiert werden, dass die auf dem Deckel und dem Pleuel eingeprägten Zahlen in die gleiche Richtung zeigen. Ziehen Sie die Muttern mit einem Drehmomentschlüssel mit einem Drehmoment von 68–75 Nm (6,8–7,5 kgf·m) an;
- - Setzen Sie den Kolben des vierten Zylinders in der gleichen Reihenfolge ein;
- - Drehen Sie die Kurbelwelle um 180° und setzen Sie die Kolben des zweiten und dritten Zylinders ein;
- - Drehen Sie die Kurbelwelle mehrmals, sie sollte sich leicht und mit geringem Kraftaufwand drehen lassen;
- - Montieren Sie den Ölpumpenhalter und die Ölpumpe am Block und befestigen Sie sie;
- - Schmieren Sie die Zwischenwellenbuchsen mit Motoröl, setzen Sie den Keil in die Nut am Zwischenwellenschaft ein und setzen Sie die Welle in den Zylinderblock ein, bis der Schaft herauskommt;
- - Montieren Sie das Ölpumpen-Antriebszahnrad mit einer Mutter auf dem Zwischenwellenschaft und ziehen Sie die Zahnradmutter fest;
- - Installieren und befestigen Sie den Zwischenwellenflansch, wobei der kleinere Durchmesser des Lochs im Flansch an den Block angrenzen sollte;
- - Schmieren Sie die Welle mit dem angetriebenen Zahnrad des Ölpumpenantriebs mit Motoröl und führen Sie sie in das Loch im Block ein, bis die Zahnräder des Ölpumpenantriebs einrasten;
- - Führen Sie die Sechskantwelle des Ölpumpenantriebs in das Loch in der Wellenhülse ein;
- - Installieren Sie die Dichtung und die Abdeckung des Ölpumpenantriebs und befestigen Sie die Abdeckung;
- - Installieren Sie die Nockenwellenantriebe in der folgenden Reihenfolge:
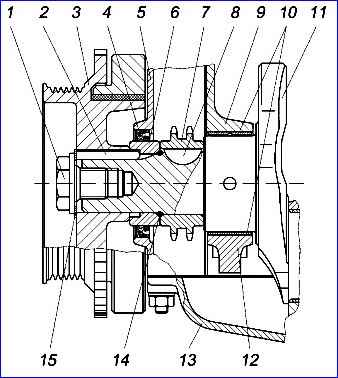
Das vordere Ende der Kurbelwelle mit einer Einzelrillenscheibe: 1 - Kupplungsbolzen; 2 - Parallelschlüssel; 3 - Dämpferscheibe mit gezahnter Synchronisationsscheibe; 4 - Manschette; 5 - Kettenabdeckung; 6 - Buchse; 7 - Sternchen; 8 – Segmentschlüssel; 9 – Zylinderblock; 10 - Hauptlagerschalen, 11 - Kurbelwelle; 12 – Hauptlagerdeckel; 13 - Ölwanne: 14 - Gummidichtring; 15 - Sicherungsscheibe
- - Kettenrad 7 auf den Kurbelwellenschaft drücken;
- - Montieren Sie den Gummidichtring 14 und die Buchse 6 mit einer großen Innenfase am Dichtring am Kurbelwellenschaft;
- - Setzen Sie den Keil der Kurbelwellenriemenscheibe in die Keilnut ein;
- - Drehen Sie die Kurbelwelle des Motors, bis die Markierung am Kurbelwellenrad mit der Markierung „M2“ am Zylinderblock übereinstimmt, was der Position des Kolbens des ersten Zylinders am oberen Totpunkt entspricht. In diesem Fall sollte die Markierung auf dem Zylinderblock symmetrisch zur Achse des Hohlraums der Kettenradzähne liegen;
- - Installieren Sie die untere Kettenführung 19, ohne die Befestigungsschrauben vollständig festzuziehen;
- - Legen Sie die Kette 6 auf das angetriebene Kettenrad 7 (Zähnezahl - 38) der Zwischenwelle und auf das Kettenrad 1 der Motorkurbelwelle. Montieren Sie das Kettenrad mit der Kette auf der Zwischenwelle, wobei die Markierung am angetriebenen Kettenrad der Zwischenwelle mit der Markierung „M1“ am Zylinderblock übereinstimmen muss und der durch den Dämpfer laufende Antriebszweig der Kette gespannt sein muss;
- - Antriebsritzel 8 (Zähnezahl - 19) der Zwischenwelle einbauen und die Ritzel mit Schrauben an der Zwischenwelle befestigen. Biegen Sie das Sicherungsblech am Rand der Bolzen;
- - Montieren Sie den Schuh 5 des hydraulischen Kettenspanners der ersten Stufe (untere Kette) des Nockenwellenantriebs;
- - Während Sie auf den hydraulischen Spannschuh drücken, spannen Sie die Kette, überprüfen Sie den korrekten Einbau der Kettenräder anhand der Markierungen und befestigen Sie abschließend den unteren Dämpfer 19.
- Nach dem Einbau der Zwischenwellen-Antriebskette darf sich die Kurbelwelle nicht drehen, bis die Nockenwellen-Antriebskette und die hydraulischen Spanner eingebaut sind;
- - Montieren Sie den Schuh 9 des hydraulischen Kettenspanners der zweiten Stufe (obere Kette) des Nockenwellenantriebs;
- - Kette 11 der zweiten Stufe des Nockenwellenantriebs auf das Antriebsritzel 8 der Zwischenwelle legen;
- - Nehmen Sie den Kettendeckel mit der Gummidichtung und prüfen Sie die Eignung der Dichtung für weitere Arbeiten. Wenn die Öldichtung abgenutzte Arbeitskanten aufweist oder die Kurbelwellenbuchse nur schwach abdeckt, ersetzen Sie sie durch eine neue. Es empfiehlt sich, den Wellendichtring mit einem Dorn in den Deckel zu drücken;
- - Füllen Sie 2/3 des Hohlraums zwischen der Arbeitskante und der Öldichtungsmanschette mit dem Schmiermittel CIATIM -221;
- - die Kette als Zweite halten In der ersten Phase nach dem Abspringen vom Zwischenwellenrad montieren und befestigen Sie die Kettenabdeckung und gleichzeitig die Generatorhalterung. Ziehen Sie die Schrauben mit einem Drehmoment von 22–27 Nm (2,2–2,7 kgf·m) an.
- - Installieren und befestigen Sie die Kühlmittelpumpe an der Kettenabdeckung, indem Sie die Schraube, mit der die Pumpe an der Kettenabdeckung befestigt ist, mit einem Drehmoment von 22–27 Nm (2,2–2,7 kgf·m) festziehen.
- - Schmieren Sie das Loch für den hydraulischen Spanner in der Kettenabdeckung mit Motoröl und installieren Sie den zusammengebauten hydraulischen Spanner 2, bis er den Schuhanschlag berührt, aber drücken Sie nicht darauf, um zu verhindern, dass die hydraulische Spannersperre funktioniert. - Installieren Sie eine geräuschdämmende Gummischeibe 3 in der Abdeckung des hydraulischen Spanners;
- - Schließen Sie die Abdeckung des hydraulischen Spanners und befestigen Sie sie mit zwei Schrauben;
- - Drücken Sie den Dorn durch das Loch in der Abdeckung des hydraulischen Spanners auf den hydraulischen Spanner, bewegen Sie ihn bis zum Anschlag und lassen Sie ihn dann los. In diesem Fall löst sich der Sicherungsring am Kolben vom Gehäuse des hydraulischen Spanners und ermöglicht den Kolben und Gehäuse bewegt sich unter der Wirkung der Feder. Der Körper bewegt sich bis zur Unterlegscheibe in der Abdeckung und die Kette wird durch den Schuh gespannt;
- - Schrauben Sie den Stopfen 4 in die Abdeckung des hydraulischen Spanners ein;
- - Installieren Sie einen Schlauch am Kühlmittelpumpenrohr, der das Pumpenrohr mit dem Thermostatgehäuserohr verbindet;
- - Tragen Sie eine dünne Schicht des Klebe- und Dichtmittels Elastosil 137-83 auf das horizontale Ende der Kettenabdeckung und die Verbindung der Kettenabdeckung mit dem Zylinderblock auf;
- - Installieren Sie die Zylinderkopfdichtung an den Blockführungsbuchsen und tragen Sie außerdem Elastosil 137-83 Klebedichtmittel auf die Oberfläche der Dichtung über der Kettenabdeckung auf;
- - Montieren Sie den zusammengebauten Zylinderkopf auf dem Block und ziehen Sie die Kopfschrauben in zwei Schritten fest – vorläufiges Anziehen mit einem Drehmoment von 40–60 Nm (4–6 kgf·m) und endgültiges Anziehen – 130–145 Nm (13,0–14). . 5 kgf m).
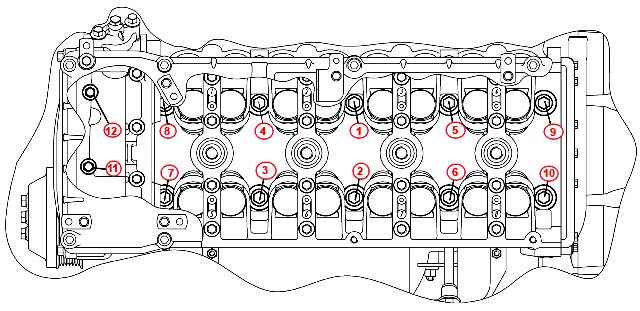
Die Reihenfolge beim Anziehen der Zylinderkopfschrauben ist in der Abbildung dargestellt. Schmieren Sie die Schraubengewinde vor dem Einbau mit Öl;
- - Lösen Sie die Schrauben und entfernen Sie die Nockenwellenabdeckungen, wischen Sie mit einer Serviette das Bett unter den Nockenwellen im Kopf und in den Abdeckungen ab;
- - Schmieren Sie die Löcher im Kopf für die Hydraulikstößel mit dem für den Motor verwendeten Motoröl und installieren Sie die Hydraulikstößel im Zylinderkopf.
Wenn Sie einen Motor reparieren, ohne die hydraulischen Stößel auszutauschen, montieren Sie diese gemäß den bei der Demontage angebrachten Markierungen; wenn der hydraulische Stößel ausfällt, muss er ersetzt werden, da er nicht repariert werden kann. Die hydraulischen Drücker müssen mit einem Saugnapf oder einem Magneten entfernt werden;
- - Montieren Sie die Nockenwellen am Zylinderkopf, nachdem Sie zuvor die Lager im Kopf, die Nocken und die Nockenwellenlagerzapfen mit Motoröl geschmiert haben.
Die Einlassnockenwelle wird so eingebaut, dass der Kettenradstift nach oben zeigt, und die Auslassnockenwelle wird so eingebaut, dass der Kettenradstift nach rechts zeigt. Aufgrund der Winkelanordnung der Nocken sind diese Positionen der Nockenwellen stabil;
- - Montieren Sie den vorderen Nockenwellendeckel mit den darin montierten Druckflanschen auf den Montagehülsen und achten Sie aufgrund der Längsbewegung der Nockenwellen darauf, dass die Druckflansche in den Nuten installiert werden;
- - Bringen Sie die Abdeckungen Nr. 3 und Nr. 7 der Nockenwellen an und ziehen Sie die Abdeckungsschrauben vor, bis die Oberfläche der Abdeckungen die obere Ebene des Zylinderkopfs berührt;
- - Montieren Sie alle anderen Abdeckungen gemäß den Markierungen und ziehen Sie die Schrauben der Abdeckung vorab fest;
- - Ziehen Sie abschließend die Schrauben der Nockenwellenabdeckung mit einem Drehmoment von 19–23 Nm (1,9–2,3 kgf·m) fest.
- - Schmieren Sie alle Nockenwellennocken mit Motoröl und überprüfen Sie die Drehung jeder Nockenwelle in den Halterungen. Drehen Sie dazu die Nockenwelle mit einem Schraubenschlüssel unter Verwendung eines speziellen Tetraeders auf der Nockenwelle, bis die Ventilfedern eines der Zylinder vollständig sind komprimiert.
Bei weiterer Drehung sollte sich die Nockenwelle unter der Wirkung der Ventilfedern selbstständig drehen, bis sie die nächsten Nocken mit Stößeln berührt;
- - Überprüfen Sie die Leichtgängigkeit der Nockenwellen und richten Sie sie dann durch Drehen so aus, dass die Ausrichtungsstifte 13 (siehe Abb. 22) unter den Kettenrädern ungefähr horizontal und in verschiedene Richtungen ausgerichtet sind.
Diese Nockenwellenpositionen sind stabil und werden durch Winkelausrichtung sichergestellt Position der Nocken;
- - Beginnen Sie mit der Überprüfung der Winkelposition der Nockenwellen von der Auslassventilwelle.
Um dies zu tun, werfen Sie die Antriebskette über das Kettenrad 16, montieren Sie das Kettenrad auf dem Flansch und dem Stift der Nockenwelle und drehen Sie die Nockenwelle im Uhrzeigersinn um den Vierkant, um den Stift und das Loch im Kettenrad auszurichten.
Spannen Sie die Antriebskette, indem Sie die Nockenwelle gegen den Uhrzeigersinn drehen, wobei die Markierung 12 am Kettenrad mit der oberen Ebene des Zylinderkopfes 17 übereinstimmen sollte. Lassen Sie die Kurbelwelle nicht rotieren;
- - Für den Winkeleinbau der Auslassnockenwelle werfen Sie die Antriebskette über das Kettenrad 14, montieren das Kettenrad auf dem Flansch und den Nockenwellenstift, wobei der Kettenzweig zwischen den Kettenrädern leicht locker sein muss.
Ziehen Sie die Kette fest, indem Sie die Nockenwelle gegen den Uhrzeigersinn drehen, sodass die Markierung 12 am Kettenrad mit der oberen Ebene des Zylinderkopfs übereinstimmt.
- - Setzen Sie den Exzenter des Kraftstoffpumpenantriebs in das Kettenrad der Einlassnockenwelle ein;
- - Installieren Sie die Schrauben, mit denen die Kettenräder (und den Exzenter an der Nockenwelle des Einlassventils) befestigt sind, und ziehen Sie sie mit einem Drehmoment von 46–74 Nm (4,6–7,4 kgf·m) fest. Halten Sie die Nockenwellen mit einem Schlüssel daran fest, dass sie sich nicht drehen quadratisch;
- - Installieren Sie den hydraulischen Spanner 10 der oberen Nockenwellen-Antriebskette auf die gleiche Weise wie den hydraulischen Spanner der unteren Kette;
- - Installieren Sie die mittleren 18 und oberen 15 Kettenstabilisatoren, ohne die Befestigungsschrauben vollständig anzuziehen;
- - Ziehen Sie die Arbeitsstränge der zweiten Kettenstufe fest, indem Sie die Kurbelwelle des Motors in Drehrichtung drehen, und befestigen Sie abschließend die Stabilisatoren der mittleren und oberen Kette.
- - Installieren Sie die Riemenscheibe bis zum Anschlag auf dem Kurbelwellenschaft und schrauben Sie die Schraube mit einem Drehmoment von 104–128 Nm (10,4–12,8 kgf·m) ein.
- - Überprüfen Sie nach Abschluss der Montage den Einbau der Nockenwellen. Drehen Sie dazu die Motorkurbelwelle zwei Umdrehungen in Drehrichtung, bis die Markierung am Kurbelwellendämpfer mit der Markierung am Kettenschutz übereinstimmt. In diesem Fall müssen die Markierungen auf den Nockenwellenrädern mit der oberen Ebene des Zylinderkopfes übereinstimmen;
- - Bei Motorreparaturen, bei denen Nockenwellen, Zylinderköpfe und Kettenräder von der Zwischenwelle entfernt werden, den Nockenwellenantrieb bei der Montage wie oben beschrieben einbauen;
- - Wenn die Zwischenwellenräder und die Kettenabdeckung bei Reparaturen nicht entfernt werden, muss vor der Demontage der Kolben des 1. Zylinders auf die OT-Position im Kompressionshub eingestellt werden, wobei die Markierung auf der Kurbelwellenriemenscheibe übereinstimmen muss Der Vorsprung am Kettendeckel und die Markierungen an den Nockenwellenrädern sollten horizontal liegen, in verschiedene Richtungen zeigen und mit der oberen Ebene der Zylindervorbereitung übereinstimmen.
Nach dem Ausbau der Nockenwellen und Zylinderköpfe kann die Kurbelwelle nur durch Zurückkehren in die Ausgangsposition oder um 2 Umdrehungen gedreht werden.
Das Drehen der Kurbelwelle um eine Umdrehung führt zu einer falschen Ventilsteuerung, auch wenn die Markierungen auf der Riemenscheibe und der Kettenabdeckung übereinstimmen.
Wenn die Nockenwellen und Kettenräder falsch eingebaut sind, stimmen die Markierungen auf den Kettenrädern nicht mit der oberen Ebene des Zylinderkopfs überein. In diesem Fall ist es notwendig, die Kettenräder zu entfernen, die Kurbelwelle eine Umdrehung in Drehrichtung zu drehen und den Einbau der Kettenräder wie oben beschrieben zu wiederholen;
- - Installieren und befestigen Sie die Riemenscheibe der Kühlmittelpumpe;
- - Montieren Sie die vordere Zylinderkopfabdeckung mit dem Antriebshebel und der Feder der Zwischenkraftstoffpumpe;
- - Installieren und befestigen Sie die vordere Zylinderkopfabdeckung;
- - Installieren Sie das Thermostatgehäuserohr im Schlauch am Kühlmittelpumpenrohr, befestigen Sie das Thermostatgehäuse am Zylinderkopf und ziehen Sie die Schlauchklemmen fest;
- - Montieren Sie den Auspuffkrümmer, die Motorhebehalterung und die Wasseransaugrohrhalterung auf den Bolzen des Auspuffkrümmers, bringen Sie die Befestigungsmuttern an und ziehen Sie sie fest;
- - Drücken Sie das Rohr der Ölstandanzeigestange hinein und installieren Sie die Anzeige;
- - Ventildeckel montieren und befestigen;
- - Installieren und befestigen Sie die obere Halterung des Generators und gleichzeitig die vordere Motorhebehalterung;
- - Installieren und sichern Sie die Spannrolle;
- - Installieren und befestigen Sie das Einlassrohr;
- - Schmieren Sie die Verbindungen des unteren Flansches des Zylinderblocks mit der Kettenabdeckung und der hinteren Abdeckung mit Elastosil 137-83 Klebedichtmittel oder UN-25-Paste;
- - Installieren Sie die Ölwannendichtung am unteren Flansch des Zylinderblocks;
- - Installieren und befestigen Sie die Ölwanne und den Kupplungsgehäuseverstärker;
- - Installieren und befestigen Sie die Abtriebs- und Kupplungsdruckplatten und zentrieren Sie die Abtriebsscheibe mit einem Dorn;
- - Motorteile und Baugruppen liefern unter Beachtung der umgekehrte Reihenfolge;
- - Nehmen Sie den Motor vom Ständer ab, installieren Sie das Kupplungsgehäuse und befestigen Sie es am Zylinderblock;
- - Schmieren Sie die Kupplungsausrückkupplungsbaugruppe mit dem Lager und platzieren Sie sie auf der vorderen Abdeckung des Getriebes;
- - Getriebe einbauen und sichern;
- - Kupplungsausrückgabel einbauen.