Der Zylinderkopf besteht aus Gusseisen, in dessen inneren Hohlräumen sich Einlass- und Auslasskanäle befinden, die durch Ventile verschlossen sind
Um die Wärmeabfuhr zu gewährleisten, verfügt der Zylinderkopf über innere Hohlräume, in denen Kühlmittel zirkuliert
Zylinderkopf 9 verfügt über eingesetzte Ventilsitze 14 und 15 aus hitzebeständiger und verschleißfester Legierung.
Auf der Oberseite des Zylinderkopfes befinden sich Zahnstangen 7, Kipphebelachse 8 mit Kipphebeln 6, Kopfdeckel 4, Ansaugkrümmer und Abdeckkappe 2, die den Ventilmechanismus verschließt.
Im Kopf auf der Seite der Kraftstoffpumpe sind vier Einspritzdüsen eingebaut, und auf der Seite des Generators ist ein Abgaskrümmer am Kopf angebracht.
Um die Verbindung zwischen Kopf und Zylinderblock abzudichten, ist eine Dichtung 10 aus Asbeststahl eingebaut.
Die Löcher für die Zylinderlaufbuchsen und den Ölkanal sind mit Stahlblech eingefasst.
Beim Zusammenbau eines Dieselmotors im Werk werden die Zylinderlöcher der Dichtung zusätzlich mit Spaltringen aus Fluorkunststoff eingefasst.
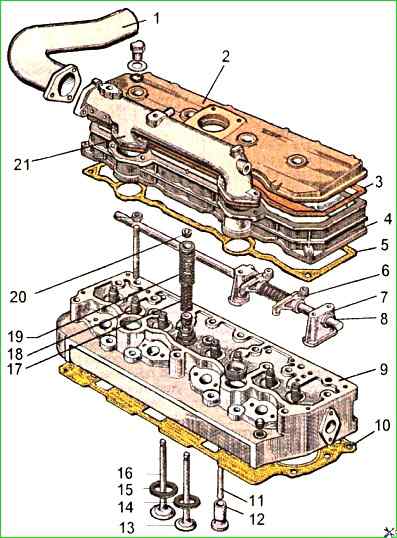
Der Zylinderkopf muss von Zunder und Kohlenstoffablagerungen gereinigt und gewaschen werden.
Risse und Undichtigkeiten in der Verschraubung der technischen Stopfen sind nicht zulässig.
Beim hydraulischen Testen des Flüssigkeitsmantels des Zylinderkopfs unter einem Druck von 0,40 ± 02 MPa für 3 Minuten sind Lecks und Tropfen nicht zulässig.
Nach dem Austausch von undichten Stopfen sollte der Zylinderkopf erneut auf Undichtigkeiten geprüft werden.
Die Unebenheit der Kontaktfläche des Zylinderkopfes zum Block sollte über die Länge des Kopfes 0,1 mm nicht überschreiten (0,05 mm bei einem neuen Kopf).
Die Unebenheit der Kontaktfläche des Zylinderkopfs zum Abgaskrümmer sollte über die gesamte Länge 0,2 mm nicht überschreiten (0,1 mm bei einem neuen Kopf).
Die Höhe des Zylinderkopfes muss mindestens 100,7 mm betragen (103-0,22 mm für einen neuen Kopf).
Die Gewindelöcher für die Stehbolzen im Zylinderkopf dürfen nicht beschädigt sein.
Die Arbeitsfasen der Ventilsitze und -scheiben müssen in einem Winkel von 45+0,5 bearbeitet werden.
Der Rundlauf der Oberfläche der Arbeitsfase des Sitzes relativ zur Oberfläche der Führungsbuchse nach der Bearbeitung sollte 0,05 mm nicht überschreiten.
Die Unrundheit der Oberfläche der Arbeitsfase der Ventilplatte im Verhältnis zur Oberfläche der Stange darf nicht mehr als 0,03 mm betragen.
Die Breite der Arbeitsfase des Sitzes sollte nach der Bearbeitung 2,0–2,2 mm betragen.
Die Höhe des zylindrischen Gürtels des Ventiltellers muss mindestens 1,5 mm betragen.
Auf -120°C abgekühlte Ventilsitze müssen in den auf 70°C erhitzten Zylinderkopf eingepresst werden.
Der Überstand der Führungsbuchse über die Ebene des Zylinderkopfes, also das Maß vom oberen Ende der Führungsbuchse bis zur Oberfläche der Zylinderaussparung für die Ventilfedern, sollte 33-1,0 mm entsprechen.
Die Ventile müssen eingeschliffen sein und fest auf den Sitzen sitzen.
Die Qualität des Läppens sollte durch das Vorhandensein eines ringförmigen Mattstreifens auf den konischen Oberflächen des Ventils und des Sitzes überprüft werden.
Die Breite des Streifens sollte 15...2,0 mm betragen; Streifenpausen sind nicht erlaubt.
Die Breite der Schlifffase des Ventilsitzes muss über die gesamte Länge gleich sein; Der Unterschied in der Breite der Bodenfase des Sitzes darf nicht mehr als 0,5 mm betragen.
Der Streifen am Ventil sollte nicht weiter als 1,0 mm vom Rand des zylindrischen Gürtels des Ventiltellers entfernt sein.
Der feste Sitz der Ventilplatte am Sitz sollte mit einem pneumatischen Gerät KI-16311 überprüft werden – bei einem Luftdruck von 0,03–0,05 MPa; Luftaustritt (Blasen) ist nicht zulässig.
Es ist möglich, den festen Sitz der Ventile an den Sitzen zu überprüfen, indem Kerosin in die Einlass- und Auslasskanäle gegossen wird. Auslaufen oder das Auftreten von Kerosintropfen unter den Ventilplatten für 2 Minuten ist nicht zulässig.
Nach dem Schleifen der Ventile an den Sitzen müssen der Zylinderkopf und die Ventile gewaschen werden, bis die Läpppaste vollständig von den Teilen entfernt ist.
Die Ventilschäfte in den Führungsbuchsen sollten sich frei bewegen können, ohne merkliches seitliches Wackeln.
Die Ventilschäfte müssen vor dem Zusammenbau mit M-10G2-Motoröl geschmiert werden.
Der Rückstand der unteren Ebenen der Einlass- und Auslassventilplatten im Verhältnis zur unteren Ebene des Zylinderkopfs sollte innerhalb von 1,05–1,25 mm liegen.
Beim Einbau in den Zylinderkopf können Stopfen mit Zink oder Titan abgedichtet werden lilami.
Die Enden der Stopfen sollten nach dem Pressen nicht über die Ebene des Zylinderkopfes hinausragen.
Die Nichtgeradheit des Ventilschafts darf über die gesamte Länge nicht mehr als 0,022 mm betragen (für ein neues Ventil - 0,015).
Risse und Haare auf den Ventiloberflächen sind nicht zulässig. 100 % der Ventile unterliegen der Kontrolle. Der Test sollte mit der Lumineszenzmethode durchgeführt werden.
Ventilfedern müssen einer 100%-Prüfung mit einem magnetischen Fehlerprüfgerät unterzogen werden; Risse an den Federn sind nicht zulässig.
Der Abstand zwischen dem Ende und dem Arbeitsgewinde der Ventilfedern sollte nicht mehr als 0,3 mm betragen, gemessen in einem Abstand von 5–10 mm vom Ende der Spule.
Die Nichtsenkrechtigkeit der Stützflächen der Ventilfedern zu ihrer Achse im freien Zustand darf entlang der Länge der Federn nicht mehr als 1° betragen.
Bei der Inspektion der Auflageflächen der Federn müssen diese auf einem Bogen von mindestens ¾ des Umfangs der Endwindung flach sein.
Nach dem Einschrauben der Stehbolzen in den Zylinderkopf sind in Bereichen ohne Gewinde Dellen bis zu einer Tiefe von 0,1 mm zulässig.
Die Cracker sollten nicht mehr als 1,4 mm über die Ebene des Ventilfedertellers hinausragen; sinken nicht mehr als 1,8 mm.
Rock-Mechanismus
Die Kipphebel-Einstellschrauben sollten über die gesamte Länge des Gewindes in die Kipphebel eingeschraubt werden, und die Sicherungsmuttern sollten fest auf die Schrauben geschraubt werden, aber ohne zu verhaken.
Die Härte der Schlagfläche des Kipphebels muss 49-57 HRC entsprechen. Die Rauheit der bearbeiteten Oberfläche des Schlagbolzens sollte Ra≤0,3 Mikrometer betragen.
Die Kipphebel müssen eng an der Auflagefläche des Zylinderkopfs anliegen.
Die Kipphebelachsstopfen müssen fest umwickelt sein und eine dichte Verbindung gewährleisten.
Die Ölkanäle der Ventilkipphebel und der Kipphebelwellen müssen gründlich gereinigt, gewaschen und mit Druckluft ausgeblasen werden.
Die Kipphebel müssen sich frei auf der Kipphebelachse drehen lassen, ohne zu verklemmen.
Der radiale Schlag der Stange im Verhältnis zu ihrer Kugeloberfläche ist bis zu 0,5 mm zulässig.
Die Unebenheit der Abdeckfläche neben dem Zylinderkopf und der Abdeckfläche neben der Abdeckkappe darf über die gesamte Länge nicht mehr als 0,25 mm betragen.
Ansaug- und Abgaskrümmer
Die Flächen der an den Zylinderkopf angrenzenden Flansche müssen in derselben Ebene liegen; Bei einer Belastung von mindestens 300 N darf die Ebenheitsabweichung nicht mehr als 0,15 mm betragen (für einen neuen Flansch - 0,1 mm).
Die Innenflächen des Ansaugkrümmers müssen sauber, frei von Kohlenstoffablagerungen und Ruß sein.
Hauptparameter der Kopf- und Gasverteilungsteile
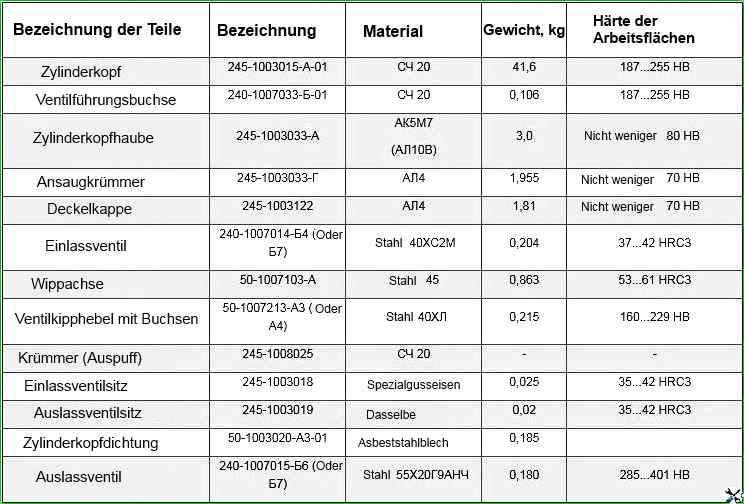
Befestigungsverbindungen des Zylinderkopfes und seiner Teile
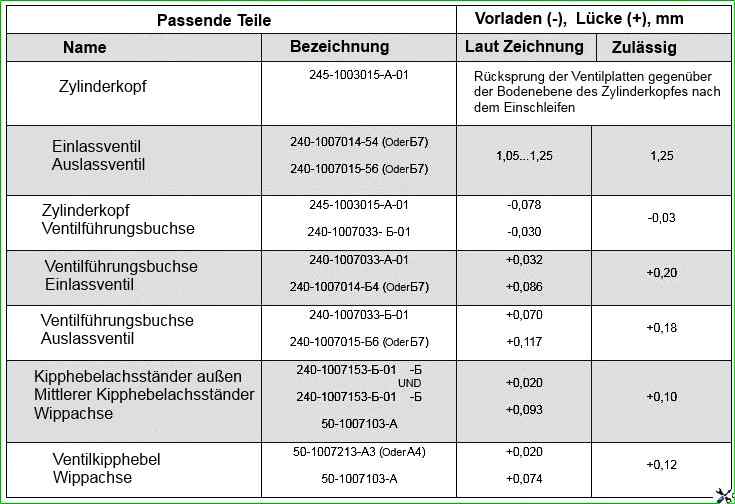