Das pneumatische System von Busbremsen besteht aus einem Kompressor, pneumatischen Geräten und Rohrleitungen
Das Diagramm des pneumatischen Antriebs des Bremssystems ist in Abbildung 1 dargestellt.
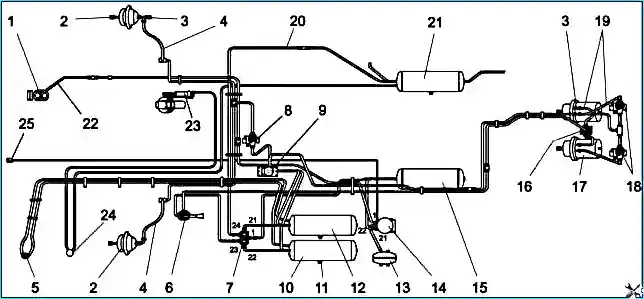
Um zu verhindern, dass die pneumatischen Geräte des Bremssystems während der ersten Betriebsphase verstopfen, können Siebe am Eingang des Bremsventils, des Trockners, des Vierkreis-Sicherheitsventils und der Modulatoren installiert werden.
Der Bus PAZ-32053-07 verwendet einen luftgekühlten Einzylinder-Kolbenkompressor
Der Kompressor wird vom Antriebsrad der Hochdruck-Kraftstoffpumpe angetrieben.
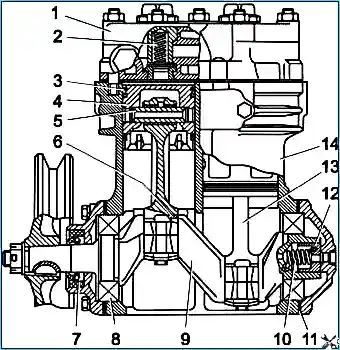
Im PAZ-4234-Bus kann sowohl ein Zweizylinder- (Abb. 2) als auch ein Einzylinder-Kompressor verwendet werden. In beiden Fällen verfügt der Kompressor über einen luftgekühlten Zylinderblock und einen wassergekühlten Zylinderkopf.
Der Kompressor wird über einen Riemen von der Kurbelwellenriemenscheibe angetrieben. Die Riemen werden durch einen speziellen Mechanismus gespannt.
Öl aus dem Schmiersystem wird über einen Schlauch dem Kurbelwellenkanal des Kompressors und den Pleuellagern zugeführt.
Kugellager, Kolbenbolzen und Zylinderwände sind spritzgeschmiert.
Öl vom Kompressor wird in die Ölwanne des Motors abgelassen.
Überprüfen Sie bei der Wartung des Kompressors dessen Befestigung an der Halterung, die Befestigung der Riemenscheibe, die Spannung der Antriebsriemen (PAZ-4234), die Befestigung des Kompressorzylinderkopfs sowie den Zustand und die Befestigung des Kompressors Kompressorauslassrohr, Schläuche zur Kühlmittelzufuhr zum Zylinderkopf (PAZ-4234) .
Der Kompressorantriebsriemen des D-245.9E2-Dieselmotors wird durch eine Rolle über den Spannmechanismus gespannt.
Lösen Sie vor dem Spannen die Sicherungsschraube der Spannrollenwelle und die Sicherungsmutter der Einstellschraube.
Dann drehen Sie die Mutter an der Einstellschraube, um die Schraube zusammen mit der Spannrolle zu bewegen.
Es wird empfohlen, die Kolben und Ventile des Kompressors einmal im Jahr während der saisonalen Wartung, jedoch nicht öfter als nach 100.000 km, von Kohlenstoffablagerungen zu reinigen.
Anzeichen für eine Fehlfunktion des Kompressors sind: Geräusche und Klopfen, übermäßige Erwärmung (mehr als 190 °C), erhöhter Ölgehalt im aus den Luftzylindern abgelassenen Kondensat.
Das Anziehen der Zylinderkopfmuttern sollte gleichmäßig in der in Abb. gezeigten Reihenfolge erfolgen. 3.
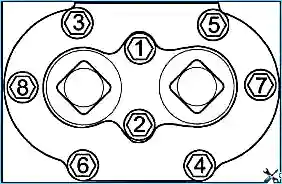
Das endgültige Anziehen erfolgt mit einem Drehmoment von (20-25) Nm.
Es ist zulässig, die Kopfmuttern gleichzeitig mit dem Enddrehmoment anzuziehen.
Achtung! Luftlecks im pneumatischen Bremssystem erhöhen die Betriebsdauer des Kompressors unter Last und verkürzen dadurch seine Lebensdauer.
Ein Lufttrockner mit eingebautem Druckregler (Abb. 4) dient dazu, die Druckluft von Feuchtigkeit und Verunreinigungen zu reinigen und den Betriebsdruck im pneumatischen Bremsantriebssystem automatisch aufrechtzuerhalten.
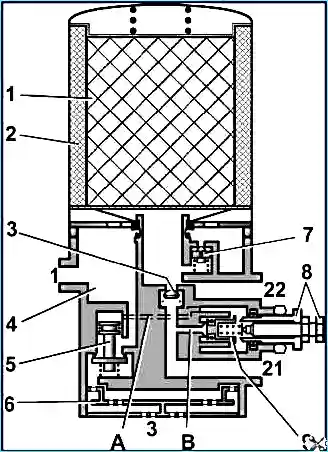
Die vom Luftkompressor zugeführte Luft passiert den Ringfilter 2 und wird dort von Verunreinigungen vorgereinigt. Dort wird die Luft abgekühlt und ein Teil der darin enthaltenen Feuchtigkeit wird in der Feuchtigkeitsabscheidekammer 4 gesammelt.
Die Luft strömt dann durch das Pulvergranulat 1, wo die Entfeuchtung stattfindet, zum Rückschlagventil 3, öffnet es und strömt über den Auslass 21 zum Vierkreis-Sicherheitsventil und dann zu den Luftbehältern.
Gleichzeitig wird über die Düse und den Auslass 22 ein Luftbehälter mit einem Fassungsvermögen von 5 Litern gefüllt, um das Trocknungselement zu regenerieren.
Der Lufttrockner verfügt über eine elektrisch beheizte Ventilbaugruppe, die eingeschaltet wird, wenn der Schlüssel im Instrumentenschalter auf Position „I“ gedreht wird. Die elektrische Heizung schaltet sich automatisch bei einer Umgebungstemperatur von weniger als +10 °C ein und schaltet sich nach dem Aufheizen auf +30 °C aus.
Um den normalen Betrieb des Trockners zu überwachen, sollten Sie täglich prüfen, ob im Zylinder hinter dem Trockner kein Kondenswasser vorhanden ist, und die Dichtheit des pneumatischen Antriebs des Bremssystems überwachen.
Wenn sich in den Behältern Kondenswasser bildet, muss das Filterelement ausgetauscht werden.
Wenn sich Öl im Kondensat befindet, ist eine Reparatur des Kompressors erforderlich, da das Einölen der Trockenmittelpulverkörnchen die Lebensdauer stark verkürzt.
Achtung! Um Ausfälle des Bremssystems zu vermeiden, sollte die Filterpatrone des Lufttrockners einmal im Jahr ausgetauscht werden, unabhängig von ihrem Zustand vor Beginn der Winterbetriebsperiode.
Der Austausch des Lufttrockner-Filterelements erfolgt in der folgenden Reihenfolge:
- Reinigen Sie die Oberfläche des Trockners von Schmutz.
- Lösen Sie die Gewindeverbindung des Auslassrohrs vom Kompressor und entlüften Sie es.
- Schrauben Sie die Filterelementpatrone ab, indem Sie sie gegen den Uhrzeigersinn drehen.
- Setzen Sie eine neue Patrone ein und schmieren Sie die Dichtung leicht mit Öl ein.
- Ziehen Sie die Kartusche von Hand mit einem Drehmoment von maximal 15 Nm fest.
- Ziehen Sie die Gewindeverbindung des Auslassrohrs fest.
Das Vierkreis-Sicherheitsventil (Abb. 5) ist so konzipiert, dass es die Versorgungsleitung in zwei Haupt- und zwei Zusatzkreise aufteilt, einen der Kreise im Schadensfall automatisch abschaltet und die Druckluftversorgung in unbeschädigten Kreisen aufrechterhält sowie zur Erhaltung der Luft in allen Kreisläufen im Falle einer Beschädigung der Versorgungsleitung.

Die Sicherheitsventilsektionen werden so eingestellt, dass zunächst die Hauptventile der Betriebsbremsanlage und des Türantriebs (in Abb. 6, Sektionen 21, 22, 24) bei einem Bypassdruck von (607-637) öffnen ) kPa, und dann öffnet das Feststellbremsventil. Bremssystem (Abschnitt 23) bei einem Bypassdruck von (656-686) kPa.
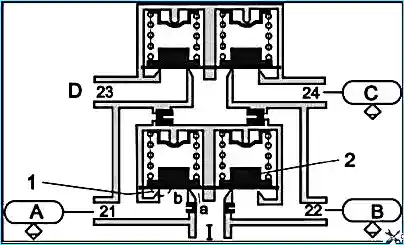
Wenn der Druck von Abschnitt 21 über ein speziell eingebautes Ventil in Abschnitt 23 entlüftet wird, wird Druckluft mit einer Rate von mindestens 60 l/min umgeleitet.
Nach dem Bypass sollte der Restluftdruck in den Energiespeichern nicht mehr als 100 kPa (1 kgf/cm 2) betragen.
Durch die Einstellung des Ventils wird verhindert, dass sich der Bus in Bewegung setzt, wenn das Pneumatiksystem soweit mit Druckluft gefüllt ist, dass das Abbremsen des Busses mit der erforderlichen Effizienz gewährleistet ist, und es besteht auch keine Möglichkeit, dass sich die Feststellbremsanlage löst des Busses, wenn der Druckpegel in Kreis 1 des Betriebsbremssystems unter den Mindestwert fällt – weniger als 390 kPa (4,0 kgf/cm 2).
Das Handventil der Feststellbremse dient zur Steuerung der Federspeicher der Feststellbremsanlage.
Wenn der Bus fährt, befindet sich der Krangriff in der äußersten vorderen Position.
Die Kranvorrichtung sorgt dafür, dass der Griff beim Loslassen automatisch in die untere Position zurückkehrt. Erst in der hintersten Position arretiert der Griff xia.
Zum Lösen von Federenergiespeichern sollte der Griff in radialer Richtung herausgezogen werden, während der Griff frei in die „entriegelte“ Position zurückkehrt.
Das Schnellablassventil ist so konzipiert, dass es das Ablassen der Luft aus den Aktuatoren beschleunigt, indem es den Weg verkürzt, den die Druckluft beim Ablassen zurücklegt.
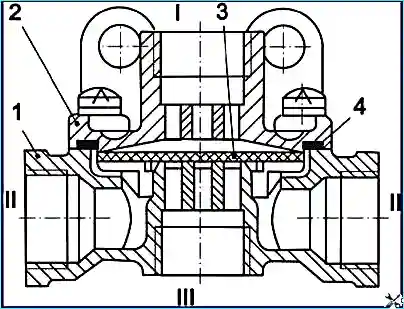
Wenn sich der Griff des Feststellbremsventils in der „gelösten“ Position befindet, gelangt Druckluft in den Auslass „I“ des Ventils (Abb. 7), die Membran 3 wird gegen den Auslasssitz im Gehäuse gedrückt; In diesem Fall werden die Kanten der Membran gebogen und die Druckluft gelangt in die Anschlüsse „II“ und weiter in die Energiespeicher.
Wenn der Druck im Anschluss „I“ abfällt, löst sich die Membran 3 unter der Wirkung der Druckluft im Anschluss „II“ vom Auslasssitz im Gehäuse 1 und wird gegen den Sitz im Deckel 2 gedrückt und blockiert so den Luftdurchtritt in Terminal „I“.
Druckluft wird über Anschluss „III“ in die Atmosphäre abgegeben.
Das Bremsventil dient zur Steuerung von Radbremsmechanismen mit Zweikreis-Bremsantrieb.
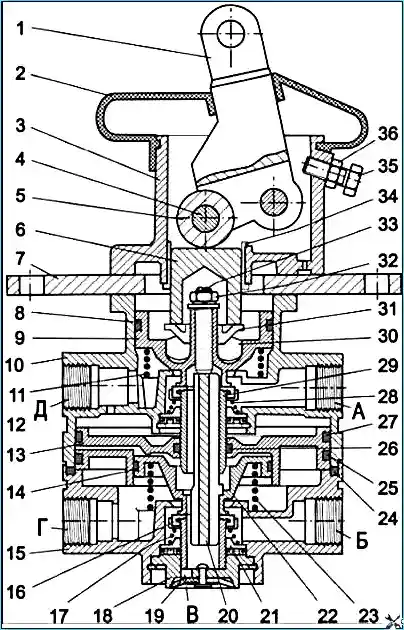
Die Anschlüsse „A“ und „B“ des Ventils (Abb. 8) sind mit den Luftbehältern zweier separater Betriebsbremsantriebskreise verbunden.
Von den Anschlüssen „G“ und „D“ strömt Druckluft zu den Bremskammern. Im Krankörper sind Bremssignalschalter eingebaut.
Von der Klemme „B“ entweicht nach Loslassen des Bremspedals Luft in die Atmosphäre.
Bei der Wartung eines Bremsventils wird die Befestigung des Ventils an der Karosseriebasishalterung überprüft, die Unversehrtheit der Schutzgummimanschette und die Dichtheit ihrer Installation überprüft und eine Diagnoseprüfung für die korrekte Funktion des Bremsventils durchgeführt Ventil.
Wenn der Wasserhahn im Winter einfriert, ist es nicht empfehlenswert, den Wasserhahn am offenen Feuer zu erwärmen, um Schäden an Gummi- und Kunststoffteilen zu vermeiden.
Zum Heizen sollten Sie warme Luft oder heißes Wasser verwenden.
Aufgrund der allmählichen Beeinträchtigung der Beweglichkeit der Bremsventilkolben während des Busbetriebs, insbesondere wenn Wasser und Öl an der Reibfläche in das Ventil gelangen, wird empfohlen, während des Betriebs eine Diagnoseprüfung der Funktion des Ventils durchzuführen TO-2.
Um dies zu tun, ohne das Ventil aus dem Bus zu entfernen, müssen Sie ein Manometer an die oberen und unteren Abschnittsanschlüsse anschließen und beim Treten des Bremspedals den Druckunterschied notieren.
Der Druckunterschied sollte 0,025 MPa nicht überschreiten. Ist diese Bedingung nicht erfüllt, muss der Kran repariert werden.
Es wird empfohlen, alle 2 Jahre eine vorbeugende Demontage des Bremsventils durchzuführen, um Gummi-O-Ringe und verschlissene Teile zu reinigen, zu schmieren und auszutauschen.
Zusammenbau und Überprüfung der Funktionsfähigkeit des Bremsventils
- Die Montage sollte unter Berücksichtigung folgender Anforderungen erfolgen:
- - Die Montage muss unter Bedingungen durchgeführt werden, die den Kontakt von abrasivem Staub usw. mit den montierten Teilen ausschließen.
- - Der Zusammenbau der Gummiteile muss sorgfältig erfolgen, um die Möglichkeit einer Beschädigung zu vermeiden. Das Vorhandensein von Schnitten, Kratzern und anderen Mängeln an Gummiteilen ist nicht zulässig.
- - Schmieren Sie alle Reibflächen der Teile mit einer dünnen Schicht des Schmiermittels CIATIM 221. Die Verwendung des Schmiermittels AZMOL ZhT-72 ist zulässig.
- Bevor Sie den oberen Kolben installieren, messen Sie den Abstand „c“ (Abb. 9) des Überstands des Kolbenschafts über dem Ventil.
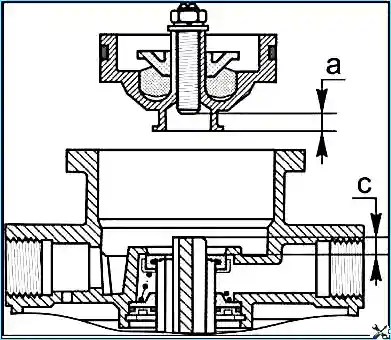
- Mit der Einstellschraube im oberen Kolben den Abstand α = (c + 0,8) mm einstellen und die Einstellschraube festziehen.
- Oberen Kolben einbauen und ggf Drücken Sie es mit einer Transportklammer.
- Bauen Sie das Gerät mit der Grundplatte und dem Hebel zusammen.
- Setzen Sie die Einstellschraube vollständig in den Hebel ein, so dass kein Spalt zwischen Rolle 4 und Stößel 5 entsteht (Abb. 10), und befestigen Sie Einstellschraube 2.
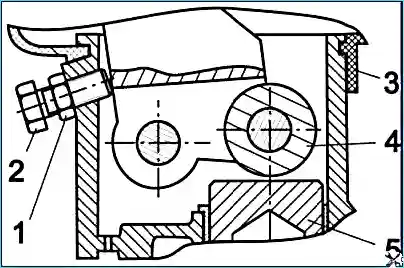
- Schließen Sie das Ventil gemäß Prüfdiagramm (Abb. 11) an das Druckluftsystem an.
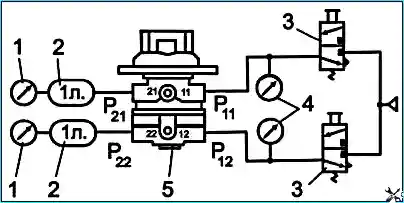
- Bewegen Sie den Hebel dreimal bis zum Anschlag (Weg von mindestens 31,2 mm). Beim Bewegen des Hebels darf es nicht klemmen und er sollte schnell in seine Ausgangsposition zurückkehren.
- Legen Sie Luft unter dem Druck P11 = P12 = 0,75 MPa (7,5 kgf/cm 2) an die Anschlüsse 11 und 12 an.
Bewegen Sie den Hebel dreimal ganz und zurück.
Der Druck an den Anschlüssen 21 und 22 sollte sich von 0 auf den Druck an den Anschlüssen 11 und 12 und zurück ändern.
- Wenn sich der Hebel um 4,7–7,4 mm bewegt (Schubhebelhub 1,9–3,0 mm), sollte Druck in Stift 21 auftreten.
Wenn der Druck P21 = 0,05 MPa (0,5 kgf/cm 2) im Auslass 21 erreicht wird, muss der Druck im Auslass 22 mindestens 0,025 MPa (0,25 kgf/cm 2).
In diesem Fall muss der Hebelhub mehr als 4,7 mm betragen (der Drückerhub muss mehr als 1,9 mm betragen).
Der Fortschritt des Druckanstiegs in Anschluss 21 relativ zum Druckanstieg in Anschluss 22 kann über den gesamten Druckbereich beibehalten werden, darf jedoch 0,025 MPa (0,25 kgf/cm 2) nicht überschreiten.
Der anfängliche Druckstoß an den Anschlüssen 21 und 22 sollte 0,02 MPa (0,2 kgf/cm 2) nicht überschreiten.
- Wenn der Druck P21 = 0,3 MPa (3,0 kgf/cm 2) in Klemme 21 erreicht wird, sollte der Hebelhub (14,5–19,9) mm betragen (Schubhebelhub (5,8–8,0)). mm).
- Wenn der Druck P21 = 0,75 MPa (7,5 kgf/cm 2) in Klemme 21 erreicht wird, sollte der Hebelhub (21–27) mm betragen (Schubhebelhub (8,4–10,8)). mm).
- Der Gesamthub des Hebels bis zum Anschlag sollte (31,1-39,1) mm betragen (Schubhub (12,5-15,7) mm).
- Wenn sich der Hebel sanft bewegt, sollte der Druck an den Anschlüssen 21 und 22 nach dem ersten Sprung allmählich ansteigen und beim Loslassen des Hebels allmählich abnehmen.
- Versorgt Klemme 12 mit Luft unter Druck P12 = 0,75 MPa (7,5 kgf/cm 2).
Bewegen Sie den Hebel bis zum Anschlag. In diesem Fall sollte sich der Druck in Anschluss 22 von 0 auf 0,75 MPa (7,5 kgf/cm 2) ändern.
- Legen Sie Luft unter dem Druck P11 = 0,75 MPa (7,5 kgf/cm 2) an Klemme 11 an.
Bewegen Sie den Hebel bis zum Anschlag. In diesem Fall sollte sich der Druck in Anschluss 21 von 0 auf 0,75 MPa (7,5 kgf/cm 2) ändern.
- Überprüfen Sie das Gerät auf Undichtigkeiten. Der Wasserhahn muss in jeder Stellung des Hebels abgedichtet sein.
Die Prüfung erfolgt bei gelöstem Hebel und einem Druck P11=P12 = 0,75 MPa (7,5 kgf/cm 2) in den Klemmen 11 und 12 sowie bei ganz durchgedrücktem Hebel und Druck P = 0,75 MPa (7,5 kgf/cm 2) in Anschluss 11. Die Luftleckage sollte in jedem Fall 8 cm 3 /min.
nicht überschreiten
Der Bremsventilantrieb ist korrekt eingestellt, wenn der volle Weg des Bremspedals, bestimmt durch die Bewegung der Mitte der Pedalauflage, (105-117) mm beträgt.
In diesem Fall sollte die Pedalplattform in der extrem gedrückten Position den Boden nicht berühren und das Bremsventil sollte vollständig geöffnet sein. Pedalspiel (18-25) mm.
Das freie Spiel des Bremspedals wird durch die Konstruktion des Bremsventils bestimmt.
Bei Bedarf (beim Aus- und Einbau eines Hahns) können Sie den Hahnantrieb wie folgt anpassen:
- - Richten Sie durch Drehen der Gabel entlang des Gewindes der Stange das Loch in der Gabel mit dem Loch im Wasserhahnhebel aus, der sich im freien Zustand befindet;
- - Schrauben Sie die Gabel eine Umdrehung von der Stange ab und installieren Sie in dieser Position den Gabelstift, stecken Sie den Stift fest und ziehen Sie die Gabelsicherungsmutter fest.
Das Steuerausgangsventil (Abb. 12) dient zum Anschluss von Steuer- und Messgeräten an den Antrieb zur Druckkontrolle.
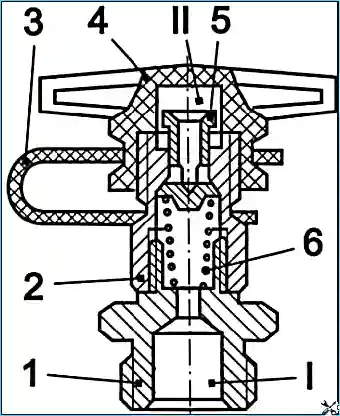
Der Bus verfügt über zwei Ventile: eines an der rechten vorderen und eines an der rechten hinteren Bremskammer.
Für den Anschluss an das Ventil verwenden Sie Schläuche und Messgeräte mit einer Überwurfmutter M16x1,5. Bei Bedarf kann das Ventil in Empfänger eingebaut werden, indem die Stopfen von den Vorsprüngen abgeschraubt werden.
Das Kondensatablassventil (Abb. 13) dient zum Zwangsablassen von Kondensat aus dem Luftbehälter des Bremsantriebs und bei Bedarf auch zum Ablassen von Druckluft aus dem Behälter.

Das Kondensatablassventil öffnet sich, wenn Sie den Drücker 3 nach oben drücken oder in eine beliebige Richtung bewegen.
Bremskammern dienen der Betätigung der Radbremsen.
Die Bremskammer mit Federenergiespeicher dient dazu, die Bremsmechanismen der Hinterachsräder bei Betätigung der Betriebs- oder Feststellbremsanlage zu aktivieren.
Wenn das Siegel gebrochen ist und der Druck im Kreislauf der Feststellbremsanlage sinkt, entweicht Luft aus dem Hohlraum unter Kolben 5 über Anschluss „I“ durch den beschädigten Teil des pneumatischen Antriebs in die Atmosphäre, Feder 4 wird freigegeben und der Bus bremst automatisch.
Um die Hinterräder mechanisch zu lösen, ist es notwendig, die Schraube 1 (Abb. 14) vom Federkraftspeicher 68 mm von der Außenfläche des Zylinders 2 abzuschrauben.
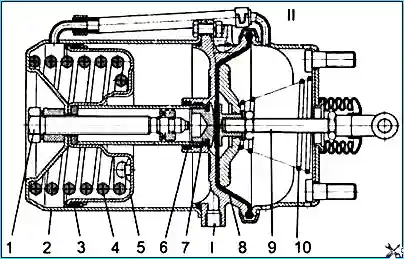
Achtung! Vor dem Lösen der Bremsen ist der Bus gegen Wegrollen zu sichern.
Achtung! Es ist verboten, den Energiespeicher ohne Verwendung einer speziellen Vorrichtung zu zerlegen, da sich im komprimierten Zustand eine starke Feder im Inneren befindet.
Achtung! Vor Inbetriebnahme des Busses sollten die Energiespeicher der Bremskammern in einen funktionsfähigen Zustand gebracht werden; dazu müssen Sie das Bremssystem mit Luft füllen, den Griff des Feststellbremsventils in die Lösestellung bringen und die Schraube festziehen 1 bis zum Anschlag (Abb. 14).
Das Hilfsbremssystem besteht aus einer Motorbremse 5, die sich im Abgasrohr 1 des Motors befindet, einem Pneumatikzylinder 3, einem Steuerventil und Rohrleitungen.
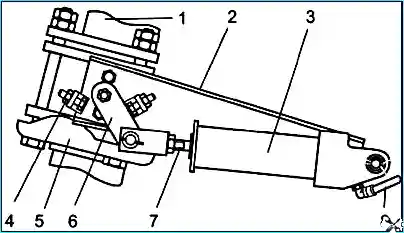
Das Zusatzbremssystem wird durch Drücken und Halten des Ventilknopfs auf dem Fahrerboden links vom Kupplungspedal aktiviert.
In diesem Fall gelangt Druckluft über Rohrleitungen vom Luftzylinder des Bremssystems in den Pneumatikzylinder 3, der über Hebel 6 den Dämpfer in der Motorbremse bewegt und dadurch das Auspuffrohr des Schalldämpfers blockiert.
Achtung! Lassen Sie das Kraftstoffregelpedal los, bevor Sie die Motorbremse betätigen.
Achtung! Das Hilfsbremssystem (Motorbremse) verlangsamt nur die Bewegung und verhindert so, dass der Bus bei langen Abfahrten schneller wird.
Sie ist nicht zum Anhalten eines Busses gedacht; sie kann nicht für Notbremsungen oder als Feststellbremse verwendet werden.
Achtung! Die Motorbremse kommt nur beim Fahren auf langen Abfahrten mit eingelegtem Gang zum Einsatz.
In diesem Fall muss ein Gang gewählt werden, bei dem die Motordrehzahl die maximal zulässige Drehzahl (2400 min -1) nicht überschreitet.
Bei der Wartung des pneumatischen Antriebs der Busbremsanlage wird die Dichtheit der Gesamtanlage und ihrer Einzelteile überprüft. Stellen mit starker Luftleckage werden nach Gehör ermittelt, Stellen mit schwacher Luftleckage werden mit einer Seifenemulsion ermittelt.
Eine Luftleckage im Betriebsbremssystem wird festgestellt, wenn das System auf Betriebsdruck gefüllt ist und das Bremspedal betätigt wird.
In diesem Fall sollte der Druckabfall 0,05 MPa (0,5 kgf/cm 2) nicht überschreiten für 15 Minuten und 0,05 MPa für 30 Minuten bei freier Stellung der Bedienelemente.
Ein Luftleck im Feststellbremssystem wird erkannt, wenn sich der Handbremsgriff in der Position „ungebremst“ befindet.
Luftleckagen aus Rohrleitungsanschlüssen werden durch Anziehen oder Ersetzen einzelner Verbindungselemente beseitigt.
Um einen Bruch der Anschlussstutzen an pneumatischen Bremsgeräten zu vermeiden, sollte das Anzugsdrehmoment der Anschlüsse, Stopfen und Muttern (30–50) Nm nicht überschreiten.
Um die Zuverlässigkeit und Zuverlässigkeit des Bremssystems zu erhöhen, wird empfohlen, alle zwei Jahre eine vorbeugende Demontage des Bremsventils durchzuführen; Bremskammern der Hinter- und Vorderradbremse, Sicherheitsventil; manuelles Bremsventil; Schnellverschlussventil; Austausch einer Ersatz-Trocknerkartusche, unabhängig von deren technischem Zustand.
Fehlerhafte Geräte, die bei einer Kontrollprüfung entdeckt werden, müssen mit Reparatursätzen repariert und auf Funktionsfähigkeit und Einhaltung der Spezifikationen überprüft werden.
Das Verfahren zum Zusammenbau und Testen der Geräte ist in speziellen Anweisungen festgelegt. Ihre Reparaturen werden von Personen durchgeführt, die über die erforderliche Schulung verfügen.
Achtung! Es ist nicht zulässig, dass Rohrleitungen durchhängen, dass sie nicht mit Teilen und Komponenten in Berührung kommen, die sich während des Betriebs bewegen und erwärmen, und dass sich Rohrleitungen nicht verbiegen, wodurch sich ihr Durchflussquerschnitt verringert.