Der Kurbelmechanismus besteht aus: einer Kurbelwelle, Kolben mit Kolbenringen und Kolbenbolzen, Pleueln, Haupt- und Pleuellagern, einem Schwungrad
Die Kurbelwelle besteht aus Stahl und hat fünf Hauptzapfen und vier Pleuelzapfen.
Die Kurbelwelle ist vorne und hinten mit Manschetten abgedichtet.
Der Kolben besteht aus einer Aluminiumlegierung.
Am Boden des Kolbens befindet sich eine Brennkammer.
Der Kolben hat im oberen Teil drei Nuten – in den ersten beiden sind Kompressionsringe und in der dritten ein Ölabstreifring eingebaut.
Unter der Nut des oberen Kompressionsrings ist ein Einsatz aus Spezialgusseisen eingegossen.
Kolbenringe
Der obere Kompressionsring besteht aus hochfestem Gusseisen, im Querschnitt hat er die Form eines gleichschenkligen Trapezes, der zweite Kompressionsring ist konisch.
Auf der Endfläche des Schlosses sind die Kompressionsringe mit „Top“ („TOP“) gekennzeichnet. Kastenförmiger Ölabstreifring mit Federexpander.
Die Pleuelstange ist aus Stahl. Zur Schmierung des Kolbenbolzens befinden sich Löcher im oberen Ende der Pleuelstange und der Buchse.
Der Verteilungsmechanismus besteht aus einer Nockenwelle, Einlass- und Auslassventilen sowie Teilen für deren Installation und Antrieb: Drücker, Stangen, Kipphebel, Einstellschrauben mit Muttern, Platten mit Crackern, Federn, Streben und Kipphebelachsen.
Die Nockenwelle wird von der Kurbelwelle über Steuerräder angetrieben
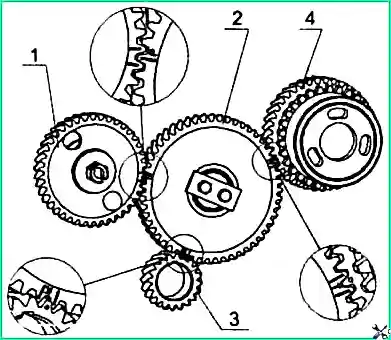
Stahlschieber. Die Nockenwellennocken sind leicht geneigt, sodass sich die Stößel während des Betriebs drehen.
Die Kipphebelachse ist hohl und verfügt über acht radiale Löcher zur Ölversorgung der Kipphebel.
Die an den Ventilführungen angebrachten Dichtungsmanschetten verhindern, dass Öl durch die Lücken zwischen den Ventilschäften und den Ventilführungen in die Dieselzylinder und den Abgaskrümmer gelangt.
Der koordinierte Betrieb der Hochdruck-Kraftstoffpumpe und des Gasverteilungsmechanismus wird durch den Einbau der Steuerräder gemäß den Markierungen gemäß Abbildung 1 gewährleistet.
Überprüfen Sie den Anzug der Zylinderkopfschrauben nach dem Ende des Einlaufvorgangs und bei jeder zweiten Wartung – 2 bei warmem Motor.
Bevor Sie den festen Sitz der Schrauben prüfen, müssen Sie die Kappe und den Zylinderkopfdeckel entfernen sowie die Kipphebelachse mit Kipphebeln und Streben entfernen.
Anschließend mit einem Drehmomentschlüssel den festen Sitz prüfen und ggf. nachziehen.
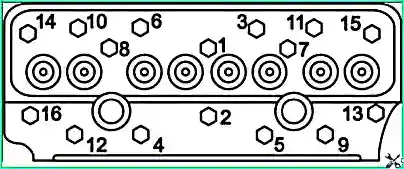
Ziehen Sie die Zylinderkopf-Befestigungsschrauben wie in Abbildung 2 gezeigt in aufsteigender Reihenfolge der Zahlen mit einem Drehmoment von (210–230) Nm fest.
Nach dem ersten Anziehen sollten Sie das Drehmoment jeder Schraube erneut überprüfen und dabei die angegebene Reihenfolge einhalten.
Nachdem Sie den festen Sitz der Schrauben überprüft haben, bauen Sie die Kipphebelachse wieder ein und stellen Sie den Abstand zwischen den Ventilen und Kipphebeln ein.
Gasverteilungsmechanismus
Überprüfen Sie die Abstände zwischen den Ventilen und Kipphebeln und passen Sie sie bei Bedarf bei jeder Wartung-2 sowie nach dem Ausbau des Zylinderkopfs, dem Anziehen der Zylinderkopfschrauben und beim Auftreten von Klopfen an.
Der Abstand zwischen dem Kipphebel-Schlagstück und dem Ende des Ventilschafts sollte bei der Überprüfung bei kaltem Motor (Kühlmittel- und Öltemperatur nicht mehr als 60 °C) betragen:
- - Einlassventile – (0,15–0,30) mm;
- - Auslassventile – (0,35–0,50) mm.
Der Abstand zwischen dem Kipphebel-Schlagstück und dem Ende des Ventilschafts sollte bei der Überprüfung bei kaltem Motor betragen:
- - Einlassventile – (0,20–0,25) mm;
- - Auslassventile – (0,40–0,45) mm.
Die Einstellung der Ventile sollte in der folgenden Reihenfolge durchgeführt werden:
Entfernen Sie die Zylinderkopfhaube und prüfen Sie die Befestigung der Kipphebelachsstreben.
Drehen Sie die Kurbelwelle am Schwungradkranz durch das Loch im Kupplungsgehäuse, bis sich die Ventile im ersten Zylinder überlappen (das Einlassventil des 1. Zylinders beginnt sich zu öffnen und das Auslassventil schließt vollständig).
Passen Sie die Abstände im 4., 6., 7. und 8. Ventil an (vom Lüfter aus gezählt).
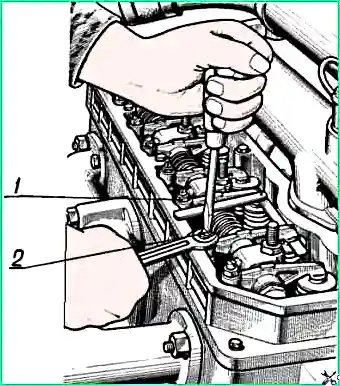
Zum Einstellen des Hecks Lösen Sie zunächst die Kontermutter 1 (Abb. 3) der Schraube 2 am Kipphebel des verstellbaren Ventils und stellen Sie durch Drehen der Schraube an der Fühlerlehre den erforderlichen Abstand zwischen Kipphebel und Ventilschaft ein.
Drehen Sie die Kurbelwelle um eine Umdrehung, stellen Sie die Überschneidung im 4. Zylinder ein und stellen Sie das Spiel im 1., 2., 3. und 5. Ventil ein.
Nachdem Sie die Lücken eingestellt haben, ziehen Sie die Muttern der Einstellschrauben mit einem Drehmoment von (40–50) Nm fest, und die Fühlerlehre sollte mit einer Kraft von (3–5) N aus der Lücke herauskommen.