Bevor Sie mit der Einstellung beginnen, spülen Sie die Ölkammer der Pumpe und des Reglers mit sauberem Dieselkraftstoff und füllen Sie frisches Motoröl bis zur Höhe der Ablassöffnung ein
Verschließen Sie für die Dauer des Tests die Ölablassschraube.
Die Inspektion und Einstellung der Kraftstoffpumpe muss von qualifiziertem Personal in einer Werkstattumgebung durchgeführt werden.
Liste der Geräte zur Überwachung von Kraftstoffpumpen: Ständer von Motorpal, Hansman oder KI-15711 mit einer Antriebsleistung von mindestens 11 kW:
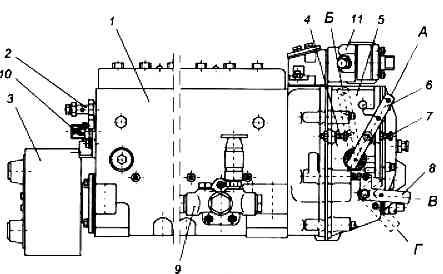
Hochdruck-Kraftstoffpumpe Modell 173: 1 - Hochdruck-Kraftstoffpumpe; 2 - Bypassventil; 3 - Dämpferkupplung; 4 - Bolzen zur Begrenzung der Höchstgeschwindigkeit; 5 - Geschwindigkeitsregler; 6 - Reglersteuerhebel; 7 - Bolzen zur Begrenzung der Mindestgeschwindigkeit; 8 - Anschlaghalterung; 9 - Kraftstoffansaugpumpe; 10 - Einstellschraube für den Startvorschub; 11 - Korrektur der Kraftstoffzufuhr; A – die Position des Hebels bei minimaler Leerlaufdrehzahl; B – Hebelposition bei maximaler Leerlaufdrehzahl; B – die Position der Halterung während des Betriebs; G – die Position der Halterung bei ausgeschaltetem Feed
- – Standausrüstung und Geräte müssen den Anforderungen von GOST 10758 entsprechen;
- – Waagen mittlerer Genauigkeitsklasse nach GOST 29329;
- - Vorrichtung zur Steuerung des Hubs des Schiebers Т9590-27;
- – ein Gerät zur Kontrolle des Beginns der Wirkung des Reglers Т9597-111.
Der Stand muss mit einem zusätzlichen System zur Versorgung der Kraftstoffpumpe mit gefiltertem Öl mit geregeltem Druck bis zu 0,4 MPa (4 kgf/cm 2) und einem Druckluftversorgungssystem mit Vorrichtung ausgestattet sein für eine stufenlose Druckregelung von 0 bis 0,15 MPa (von 0 bis 1,5 kgf/cm 2).
Pumpentests sollten mit gefiltertem Dieselkraftstoff der Klasse L gemäß GOST 305-82 oder einer kalibrierten (Prozess-)Flüssigkeit, bestehend aus einer Mischung mit Industrieöl gemäß GOST 20799-88, Luftfahrtöl gemäß GOST, durchgeführt werden 21743-76 oder Leuchtkerosin gemäß TU 38.401-58-10-90 mit einer Viskosität von 5–6 mm 2/s (cSt) bei einer Temperatur von (20 ± 5) °C.
Es ist erlaubt, eine Mischung von Arbeitsflüssigkeiten zu verwenden, die aus 40 % RZh-3 TU 38.101.964 und 60 % RZH-8 TU 38.101.883 mit einer Viskosität von 5-6 mm 2/s (cSt) bei einer Temperatur von (20±5)°С.
Die Temperatur des Kraftstoffs, gemessen am Auslassanschluss des Ständers mit der Kraftstoffleitung zur getesteten Pumpe, sollte bei der Kontrolle der Größe und Ungleichmäßigkeit der zyklischen Zufuhren (32 ± 2) ° C betragen.
Bevor Sie die Pumpe auf dem Ständer montieren, prüfen Sie, dass die Nockenwelle kein axiales Spiel aufweist. Wenn Spiel vorhanden ist, stellen Sie einen Presssitz von 0,01–0,07 mm sicher, nachdem Sie das Spiel der Nockenwelle auf 0,03–0,09 mm durch den Einbau von Unterlegscheiben eingestellt haben, kontrolliert durch eine Kraft von 90–100 N (9–10 kgf), und entfernen Sie dann zwei Unterlegscheiben mit einer Dicke von 0,05 mm.
Beim Anziehen der Deckelschrauben muss sich die Nockenwelle in den Lagern frei drehen lassen.
Die Überprüfung und Einstellung der Kraftstoffpumpe sollte mit einem Satz Einspritzdüsen des Modells 26-03С mit einem effektiven Durchflussquerschnitt μf = 0,244 mm 2 durchgeführt werden.
Es ist erlaubt, die Kraftstoffpumpe mit einem funktionierenden Satz Einspritzdüsen zu überprüfen und einzustellen. Jede Düse muss dem entsprechenden Abschnitt der Kraftstoffpumpe zugeordnet und anschließend in den mit diesem Abschnitt verbundenen Motorzylinder eingebaut werden.
Für das Bankset der Hochdruck-Kraftstoffleitungen sollten Rohre mit einer Länge von 415 ± 3 mm verwendet werden, der Unterschied im Durchsatz der Kraftstoffleitungen, aus denen das Bankset besteht, sollte 0,5 mm 3/cycle.
Bestimmen Sie den Durchsatz der Kraftstoffleitung an einem Hochdruckabschnitt, mit einer Düse und an einem Tischentschäumer.
Bevor Sie prüfen und einstellen, müssen Sie sicherstellen, dass das Niederdrucksystem und der Ölhohlraum der Hochdruck-Kraftstoffpumpe dicht sind. Dazu gilt:
Verschließen Sie die Öffnung des Bypass-Ventils, die Auslassöffnung der Kraftstoffansaugpumpe, die Anschlüsse der Hochdruck-Kraftstoffpumpe, die Ölversorgungsschraube des Boost-Korrektors, die Kraftstoffabsaugöffnung für den Elektrobrenner und installieren Sie die Rackabdeckung.
Schließen Sie einen Schlauch mit einem Innenvolumen von nicht mehr als 25 cm 3 (Innendurchmesser nicht mehr als 8 mm) fest an die Ölablassschraube im Gehäuse der Einspritzpumpe an.
Tauchen Sie das freie Ende des Rohrs maximal 20 mm tief in ein Gefäß mit Kraftstoff ein.
Versorgen Sie den Kraftstoffeinlass der Einspritzpumpe und den Kraftstoffeinlass der Kraftstoffansaugpumpe mit Druckluft.
Die Einspritzpumpe gilt als geeignet, wenn bei einem gleichmäßigen (innerhalb von 10-20 s) Druckanstieg im System von 0 auf 0,5 MPa (von 0 auf 5 kgf/cm 2) Es werden keine Blasen in der Luft beobachtet Kraftstofftank.
Schließen Sie Druckluft an die Ölablassschraube an und tauchen Sie die Einspritzpumpe in einen Behälter mit Dieselkraftstoff.
Die Einspritzpumpe gilt als versiegelt, wenn bei einem Druck von 0,01–0,015 MPa (0,1–0,15 kgf/cm 2) 20s lang keine Luftblasen durch die Anschlüsse der Einspritzpumpe beobachtet werden. mit Ausnahme der folgenden Verbindungen: die Klemmschraube der Schiene – das Einspritzpumpengehäuse, die Achse des Ladedruckkorrekturhebels – das Membrangehäuse.
Bei der Überprüfung der Kraftstoffpumpe wird Folgendes überwacht:
- – Beginn der Kraftstoffzufuhr durch Pumpenabschnitte;
- - die Menge und Ungleichmäßigkeit der Kraftstoffzufuhr.
Der Beginn der Kraftstoffzufuhr durch die Pumpenabschnitte wird durch den Hub des Stößels, den Drehwinkel der Pumpennockenwelle bei Drehung im Uhrzeigersinn, von der Antriebsseite aus gesehen, bestimmt, wobei die Zahnstangenposition dem entspricht Nennvorschub, d.h. Position, in der die Schiene um (11 ± 1) mm über das Ende der Pumpe hinausragt.
Der Beginn der Kraftstoffzufuhr durch den ersten Abschnitt der Pumpe muss dem Hub des Stößels 5,2 ± 0,05 mm entsprechen.
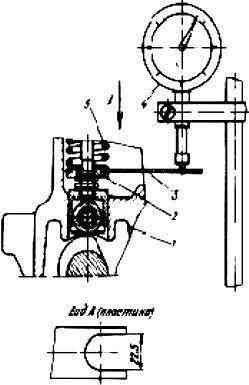
Ein Gerät zur Überprüfung des Schieberhubs: 1 - Gehäuse der Hochdruck-Kraftstoffpumpe; 2 - untere Platte der Drückerfeder; 3 - Teller; 4 - Indikator; 5 - Drückerfeder
Messen Sie den Hub des Schiebers mit einem Indikator (Abb. 2).
In dem Moment, in dem die erste Sektion mit der Kraftstoffzufuhr beginnt, müssen die Markierungen auf der Einspritzstartanzeige und auf dem Torsionsschwingungsdämpfer übereinstimmen. Die Abweichung der Markierungen sollte 0,5° nicht überschreiten.
Die Auslieferung der Pumpenabschnitte sollte in der folgenden Reihenfolge erfolgen (in Grad der Nockenwellendrehung):
- Abschnitt Nr. 1 – 0° Abschnitt Nr. 4 – 180°
- Abschnitt Nr. 3 – 45° Abschnitt Nr. 5 – 225°
- Abschnitt Nr. 6 – 90° Abschnitt Nr. 7 – 270°
- Abschnitt Nr. 2 – 135° Abschnitt Nr. 8 – 315°
Die Abweichung der Winkel der Nockenwelle, die dem Beginn der Kraftstoffförderung durch die Pumpenabschnitte entsprechen, relativ zum geometrischen Beginn der Kraftstoffeinspritzung durch den ersten Abschnitt der Pumpe sollte ± 30 Minuten betragen, nicht mehr.
Die Einstellung des Beginns der Kraftstoffzufuhr erfolgt durch Dichtungen, die unter den Flanschen des Abschnittskörpers angebracht sind. Ihre Anzahl und Dicke muss auf beiden Seiten gleich sein, wobei die dickste Dichtung oben liegen sollte.
Wenn die Dicke der Dichtungen erhöht wird, beginnt die Kraftstoffzufuhr später, wenn die Dicke verringert wird, beginnt sie früher.
Um Schäden an der Pumpe zu vermeiden, sollte die Mindestdicke der Dichtungen nicht weniger als 0,6 mm betragen.
Überprüfen und stellen Sie die Menge und Gleichmäßigkeit der Kraftstoffzufuhr in der folgenden Reihenfolge ein:
1. Überprüfen Sie den Druck zu Beginn des Öffnens der Auslassventile. Er sollte 0,06 ± 0,04 MPa (0,6 ± 0,4 kgf/cm 2) betragen.
Der Druck zu Beginn des Öffnens der Auslassventile sollte in dem Moment überwacht werden, in dem der Kraftstoff aus der Kraftstoffleitung mit einem Innendurchmesser von (2 ± 0,05) mm zu fließen beginnt, wobei der Druck an dieser Stelle allmählich ansteigt Einlass zur Kraftstoffpumpe und die Rackposition, die der ausgeschalteten Kraftstoffversorgung entspricht.
2. Überprüfen Sie den Kraftstoffdruck in der Leitung am Einlass zur Kraftstoffpumpe. Der Druck sollte 0,175 ± 0,025 MPa (1,75 ± 0,25 kgf/cm 2) bei der Nenngeschwindigkeit der Nockenwelle und dem Steuerhebel gegen die Höchstgeschwindigkeitsbegrenzungsschraube betragen.
Schrauben Sie bei Bedarf den Stopfen des Bypassventils ab und stellen Sie den Öffnungsdruck mit Unterlegscheiben ein.
3. Überprüfen Sie die Zahnstangenwegreserve. Unter der Gangreserve der Zahnstange versteht man den freien Weg der Zahnstange (Spiel) in Richtung der Abschaltung des Vorschubs bei 450-600 min-1 und wenn der Reglersteuerhebel am Minimum anliegt Geschwindigkeitsbegrenzungsschraube.
Wenn keine Zahnstangenwegreserve vorhanden ist, ist es notwendig, die Leistungseinstellschraube bis zum Anschlag herauszudrehen und dann die Zahnstangenwegreserve innerhalb von 1-1,3 mm mit der Backstage-Schraube einzustellen und zu arretieren.
Das Herausragen der Jochschraube über das äußere Ende der Reglerabdeckung hinaus ist nicht zulässig
4. Überprüfen Sie den Beginn des Abschaltens der Startkraftstoffzufuhr bei 230–250 min -1, wenn der Steuerhebel zu Beginn der Zahnstangenbewegung auf der Mindestgeschwindigkeitsbegrenzungsschraube ruht.
Wenn Sie die Geschwindigkeit erhöhen müssen, entfernen Sie den Federhaken vom Zahnstangenhebel und schrauben Sie ihn in die Feder. Um die Geschwindigkeit zu reduzieren, dreht man den Haken aus. Setzen Sie anschließend den Haken auf den Schienenhebel.
5. Überprüfen Sie den Wert der durchschnittlichen Startkraftstoffzufuhr, die innerhalb von 210–240 mm 3/Zyklus bei einer Pumpennockenwellendrehzahl von 80 ± 10 min -1 liegen sollte.
Eingestellt durch die Startvorschub-Einstellschraube 10 (Abb. 1). Beim Herausdrehen des Bolzens aus der Schiene verringert sich der Anfangsvorschub, beim Eindrehen erhöht er sich.
6. Während der Steuerhebel an der Schraube zur Begrenzung der Höchstgeschwindigkeit anliegt, prüfen Sie die entsprechende Drehzahl der Nockenwelle der Pumpe Der Beginn des Auswurfs der Zahnstange, bestimmt durch den Moment, in dem die Zahnstange beginnt, sich in Richtung Auslauf zu bewegen.
Der Auswurf des Racks sollte mit einer Geschwindigkeit von 1080-1100 min -1 beginnen.
Die Einstellung sollte mit der Höchstgeschwindigkeitsbegrenzungsschraube erfolgen.
7. Überprüfen Sie die Geschwindigkeit, die dem Ende des Zahnstangenauswurfs entspricht und durch den Moment bestimmt wird, in dem die Kraftstoffzufuhr durch die Einspritzdüsen stoppt.
Das Ende des Abschaltens sollte mit einer Geschwindigkeit erfolgen, die 60–120 min-1 höher ist als die Geschwindigkeit, mit der der Rack-Auswurf beginnt.
Mit der Schraube des zweiarmigen Hebels einstellen.
Beim Einschrauben nimmt die Geschwindigkeit des Auswurfendes des Racks ab, beim Ausschrauben erhöht sie sich. Gleichzeitig ändert sich auch der Abschaltbeginn, so dass eine nachträgliche Überprüfung und Anpassung erforderlich ist.
8. Überprüfen Sie die durchschnittliche zyklische Kraftstoffzufuhr, die Erhöhung der durchschnittlichen zyklischen Zufuhr und die Ungleichmäßigkeit des Kraftstoffs und stellen Sie sie bei Bedarf mit dem Werkbanksatz von Einspritzdüsen Modell 26-03 C ein, wobei der Steuerhebel des Reglers auf der Höchstgeschwindigkeitsbegrenzungsschraube ruht Bereitstellung in Abschnitten, die wie folgt lauten sollten:
Drehfrequenz der Nockenwelle, min -1 – Durchschnittliche zyklische Kraftstoffzufuhr durch Pumpenabschnitte, mm 3 / Zyklus – Ungleichmäßige Kraftstoffzufuhr durch Pumpenabschnitte, % nicht mehr
- 1030±10 - 152–158 - 5;
- 900±10 - q - (2–8) - -;
- 650±10 - q - (5–11) - 8;
- 500±10 - 152 - 162 - -
q – durchschnittliche zyklische Kraftstoffzufuhr durch die Pumpe im Nennmodus.
Bei der Überprüfung der Pumpe am Kontrollstand ist eine zusätzliche Abweichung des durchschnittlichen zyklischen Durchflusses von ± 1 % zulässig.
Der Wert des durchschnittlichen zyklischen Vorschubs wird als Summe des Vorschubs aller Abschnitte dividiert durch die Anzahl der Abschnitte berechnet.
Die ungleichmäßige Kraftstoffversorgung nach Abschnitten wird nach folgender Formel berechnet:
- - qcmax – maximale zyklische Kraftstoffzufuhr nach Abschnitten, mm3/Zyklus;
- - qcmin – minimale zyklische Kraftstoffzufuhr nach Abschnitten, mm3/Zyklus.
8.1. Passen Sie den Wert des durchschnittlichen zyklischen Vorschubs im Nennmodus mit der Nennvorschubschraube an: Wenn Sie die Schraube im Uhrzeigersinn drehen, verringert sich der Vorschub, gegen den Uhrzeigersinn erhöht er sich.
Regulieren Sie die Gleichmäßigkeit der zyklischen Kraftstoffzufuhr durch jeden Pumpenabschnitt, indem Sie das Abschnittsgehäuse relativ zum Pumpengehäuse drehen, nachdem Sie die Flanschbefestigungsmuttern gelöst haben.
Durch Drehen des Abschnitts im Uhrzeigersinn wird der Taktvorschub erhöht, gegen den Uhrzeigersinn verringert. Ziehen Sie nach der Einstellung die Flanschmuttern fest an.
- 8.2. Die Erhöhung des durchschnittlichen zyklischen Vorschubs bei einer Drehzahl von 800 min -1 passt den Körper des Negativkorrektors an. Verriegeln Sie das Gehäuse nach der Einstellung sicher.
- 8.3. Die Erhöhung des durchschnittlichen zyklischen Vorschubs bei einer Drehzahl von 650 min -1 entspricht dem maximalen Drehmoment und 500 min -1 wird mit der negativen Korrekturmutter eingestellt.
Beim Anziehen der Mutter wird der Vorschubschritt verringert, beim Herausdrehen erhöht. Kontern Sie die Mutter nach der Einstellung sicher.
Überprüfen Sie die Kraftstoffpumpen gemäß den Punkten 1-8 bei fehlendem Luft- und Öldruck im Ladedruckregler.
9. Überprüfen Sie dazu die Funktion des Kraftstoffverstärkungskorrektors:
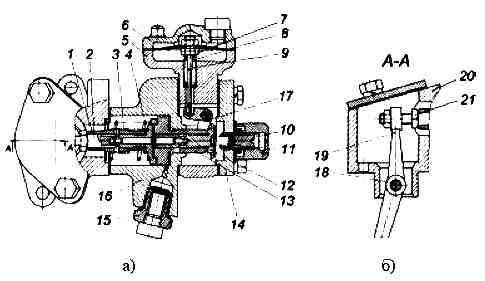
Kompressor für die Kraftstoffzufuhr: a) horizontaler Abschnitt: b) vertikaler Abschnitt; 1 - Anschlaghülse; 2 - Betonung; 3 - Ärmelfeder; 4 - Kolbenfeder; 5 - Membrankörper; 6 - Membranabdeckung; 7 - Kontermutter der Membranstange; 8 - Frühling; 9 - Stab mit Membran; 10 - Korrekturfedergehäuse; 11 - Korrekturfeder; 12 - Spule; 13 - Kolben; 14 - Korrektorabdeckung; 15 - Ölversorgungsanschluss; 16 - Korrektorgehäuse; 17 - Hebel; 18 - Hebelachse; 19 - Hebel; 20 - Abstandshalter; 21 - Hebeleinstellschraube
- 9.1. Spülen Sie den Netzfilter des Anschlussstücks 15 (Abb. 3) in sauberem Benzin aus und blasen Sie ihn gründlich mit Druckluft aus.
- 9.2. Reinigen Sie das Kalibrierungsloch im Korrektorkörper mit einem weichen Draht mit einem Durchmesser von (0,5–0,7) mm.
- 9.3. Überprüfen Sie die Dichtheit des Membranhohlraums. Führen Sie dazu Luft mit einem Druck von 0,06 ± 0,01 MPa (0,6 ± 0,1 kgf/cm 2) dem Loch in der Abdeckung des Membrangehäuses zu.
Wenn der Zuluftkanal vollständig geschlossen ist, sollte der Druckabfall im Membranhohlraum über einen Zeitraum von 2 Minuten 0,01 MPa (0,1 kgf/cm 2) nicht überschreiten.
- 9.4. Im Schwerpunkt des Knurrens ha Kontrolle im Bolzen, der die Höchstgeschwindigkeit begrenzt, stellen Sie die Geschwindigkeit auf 650 min -1 ein und bringen Sie Öl unter einem Druck von 0,275 ± 0,025 MPa (2,75 ± 0,25 kgf/cm 2).
Um den Boost-Korrektor in Betrieb zu nehmen, schalten Sie die Kraftstoffzufuhr einmal mit der Backstage-Halterung ab und bewegen Sie die Halterung dann in die Position "Off Supply".
- 9.5. Überprüfen Sie den Wert der zyklischen Kraftstoffzufuhr bei verschiedenen Luftdrücken im Membranhohlraum, der sein sollte:
Durchschnittliche zyklische Kraftstoffzufuhr durch Pumpenabschnitte, mm 3/Zyklus bei Luftdruck im Hohlraum der Korrekturmembran, MPa (kgf/cm 2)
- 0,05–0,1 (0,5–1,0); 0,035 ± 0,001 (0,35 ± 0,01); 0 - 0,02 (0 - 0,2)
- q - (5 - 11)*; (140 - 146)*; (132 – 138)*
q ist die durchschnittliche zyklische Kraftstoffzufuhr durch die Pumpe im Nennmodus.
Die mit einem (*) gekennzeichneten zyklischen Zufuhren müssen bei einem Öldruck am Korrektoreinlass von 0,275 ± 0,025 MPa (2,75 ± 0,25 kgf/cm 2) bereitgestellt werden.
Wenn der Öldruck auf 0,15 MPa (1,5 kgf/cm 2) abfällt, darf der tatsächliche zyklische Vorschub um 3 mm 3/ geändert werden Zyklus aus gegebenen Werten.
Wenn sich der Luftdruck am Korrektoreinlass von 0,06 MPa (0,6 kgf/cm 2) auf 0,14 MPa (1,4 kgf/cm 2) ändert), Die zyklische Kraftstoffzufuhr muss konstant sein und dem mit (*) gekennzeichneten Wert entsprechen und die Änderung ihres Wertes darf ± 2 mm 3/Zyklus nicht überschreiten.
Sollten die gemessenen Werte der zyklischen Einspeisungen von den angegebenen abweichen, ist eine Neujustierung des Umwerters erforderlich.
Die Einstellung der Menge der zyklischen Kraftstoffzufuhr bei einem Luftüberdruck auf der Membran von 0 MPa (kgf / cm 2) erfolgt durch die Einstellschraube 21 (Abb. 3).
Beim Eindrehen einer Schraube erhöht sich die Vorschubgeschwindigkeit, beim Herausschrauben verringert sie sich. Kontern Sie die Schraube nach der Einstellung mit einer Mutter.
Die Menge der zyklischen Kraftstoffzufuhr bei mittleren Luftdrücken an der Membran wird durch das Federgehäuse 10 reguliert (Abb. 3).
Wenn das Federgehäuse eingeschraubt ist, verringert sich die Kraftstoffzufuhrmenge, wenn es herausgedreht wird, erhöht es sich. Kontern Sie das Federgehäuse nach der Einstellung mit einer Mutter.
Bevor Sie eine verschlissene Membran ersetzen (falls erforderlich), messen Sie den Überstand des Schafts vom unteren Ende der Mutter an der Membran mit der Schaftbaugruppe.
Danach ersetzen Sie die Membran und montieren sie mit einer Stange mit dem gleichen Überstand der Stange mit einer Genauigkeit von 0,1 mm, während die Senkung des Endes der Spule 12 relativ zum Ende des Kolbens 13 0,2 betragen sollte -0,9 mm, wenn zwischen Endkolben und Korrektorkörper kein Spalt vorhanden ist.
Wenn Sie den Boost-Korrektor nach der Demontage (falls erforderlich) am Regler installieren, bewegen Sie die Pumpenschiene mit der Backstage-Halterung in die äußerste Aus-Position, installieren Sie den Boost-Korrektor im Reglergehäuse und lassen Sie dann die Halterung los.
Überprüfen Sie die Einstellung des Boost-Korrektors auf das Vorliegen einer Unterbrechung der Kraftstoffzufuhr durch den Regler.
10. Begrenzen Sie mit der Leistungseinstellschraube, wenn der Steuerhebel an der Schraube zur Begrenzung der Höchstgeschwindigkeit anliegt, die nominalen zyklischen Vorschübe, die wie folgt sein sollten:
Pumpennockenwellendrehzahl, min. -1
Durchschnittliche zyklische Kraftstoffzufuhr durch Pumpenabschnitte, mm 3/Zyklus 1030±10 136 – 142
Verriegeln Sie die Leistungseinstellschraube sicher.
Überprüfen Sie die Bewegungsreserve der Zahnstange, wenn der Reglersteuerhebel an der Mindestgeschwindigkeitsbegrenzungsschraube anliegt und bei einer Nockenwellendrehzahl von 500 min -1.
Der Spielraum der Schiene sollte mindestens 0,5 mm betragen.
11. Überprüfen Sie die Abschaltung des zyklischen Vorschubs durch den Verbindungsbügel bei einer Drehung um 40-45° aus der Ausgangsposition.
Die Kraftstoffzufuhr von den Einspritzdüsen aller Abschnitte der Kraftstoffpumpe sollte bei jeder Geschwindigkeit und in jeder Position des Reglersteuerhebels vollständig unterbrochen sein.
Setzen Sie die Kappen auf die Kraftstoffpumpe und den Regler und verschließen Sie diese.
Setzen Sie eine Dichtung auf die Einstellschraube für die maximale Geschwindigkeit.
Montieren Sie die Kraftstoffpumpe in vertikaler Position am Motorblock und ziehen Sie die Befestigungsschrauben gleichmäßig fest, um ein Blockieren der Pumpe zu vermeiden.
Das endgültige Anzugsdrehmoment der Pumpenbefestigungsschrauben beträgt 30–40 Nm (3–4 kgcm). Schließen Sie die Kraftstoffleitungen an, nachdem Sie die Kraftstoffpumpe befestigt haben.