During operation, as well as due to errors in the manufacture of timing gear drive parts or due to unskilled repairs of the timing drive, a significant deviation of the valve timing from the specified values is possible
The correct valve timing is one of the most important factors affecting the power, torque and economic performance of the engine.
Therefore, when the traction properties of the engine decrease, the operating fuel consumption increases and the engine becomes unstable, it becomes necessary to check and, if necessary, set the valve timing correctly.
For this purpose, a set of equipment developed at ZMZ is used.
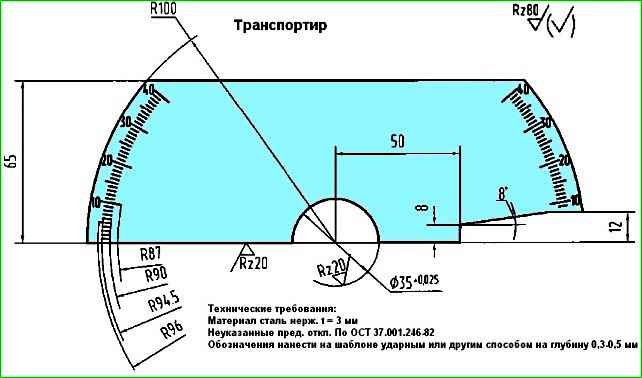
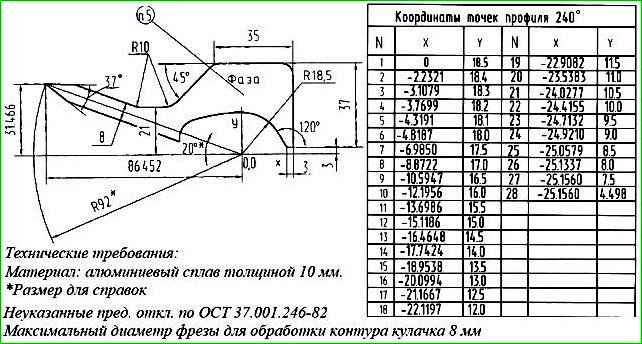
The kit includes: protractor (Figure 1), template (Figure 2) with cam profile and arrow
Also a jig for drilling additional holes for the pin in the camshaft sprockets (Figure 3).
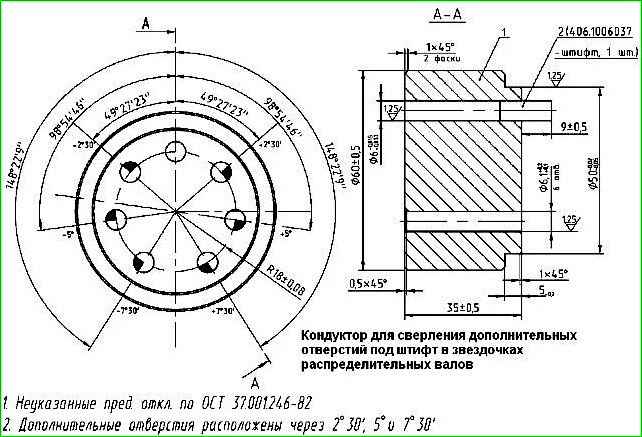
Checking and adjusting the valve timing can be carried out on an engine installed on a car; to control the valve timing, you must:
- 1. Disconnect the crankcase ventilation hose from the valve cover pipe by loosening the fastening clamp.
- 2. Disconnect the wire connectors from the ignition coils.
- 3. Remove the tips from the spark plugs with seals and high voltage wires.
- 4. release from the brackets and remove the wiring harness from the valve cover.
- 5. Remove the valve cover with gasket, spark plug well seals, ignition coils and high-voltage wires assemblies by unscrewing eight bolts (head “12”, extension and wrench).
- Leave the bolts, washers and brackets for the wiring harness in the holes in the cover. (The picture shows the stages using the ZMZ-4062 as an example)
- 6. Set the piston of the 1st cylinder to TDC of the compression stroke by turning the crankshaft in the direction of rotation (clockwise) until the mark on the crankshaft damper pulley coincides with the indicator rib (in the form of a boss) on the chain cover.
Attention! Rotating the crankshaft counterclockwise is not permitted.
In this case, the camshaft cams of the 1st cylinder and the marks on the camshaft sprockets must be located according to the diagram
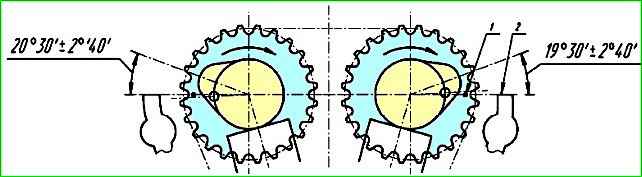
If the tops of the cams and marks are located inward, then it is necessary to turn the crankshaft one more revolution.
Precise installation of the piston of the 1st cylinder at TDC can be done using a dial indicator, which is installed and secured in the spark plug hole of the 1st cylinder.
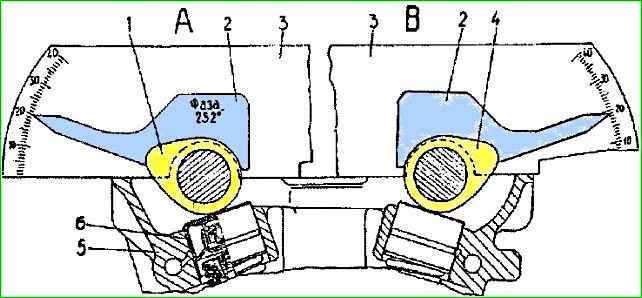
7. Install protractor 3 (Figure 6) behind the first cam of the intake camshaft - view “A”, placing it between the cam and the camshaft support cover.
Pressing protractor 3 to the upper plane of cylinder head 5, attach and press template 2 tightly to the surface of the first cam.
At the same time the template marker should be located on the protractor mark 20˚30′± 2˚40′
When measuring, the leading branch of the chain in the area of the upper damper (between the camshaft sprockets) must be tensioned and held in this state by turning the intake camshaft counterclockwise with a 27 wrench using the square on the shaft body.
In this case, turning the exhaust camshaft is not allowed.
Check the angular position of the first cam of the exhaust camshaft in the same way - view “B”.
The template arrow should point to the protractor mark 19°30′±2°40′.
When measuring, the drive branch of the chain in the area of the middle damper (between the camshaft sprocket and the drive sprocket of the intermediate shaft) must be tensioned and held in this state by turning the exhaust camshaft counterclockwise with a 27 wrench at the square on the shaft body.
In this case, turning the intermediate and crankshafts is not allowed.
With these values of the angular position of the first camshaft cams, the best technical and economic performance of the engine is achieved.
If the deviations in the angular position of the camshaft cams exceed the permissible ±2°40′, adjustment of the valve timing is required.
To do this, you need to perform the following work on the engine:
- 1. Remove the front cylinder head cover by unscrewing the four bolts (key “12”).
- 2. Remove the upper hydraulic tensioner (in the cylinder head) by unscrewing the two bolts (head “12”, extension and knob) securing the hydraulic tensioner cover, remove the cover with the soundproofing washer.
- 3. Remove the upper and middle chain guides by unscrewing two bolts each (key “6” for bolts with a hexagonal socket).
- 4. Remove the camshaft sprockets by unscrewing their fastening bolts one by one (wrench “12”), while holding the shafts with a wrench “27” by the square on the camshaft body.
Keep the chain removed from the camshaft sprockets from jumping off the intermediate shaft sprocket.
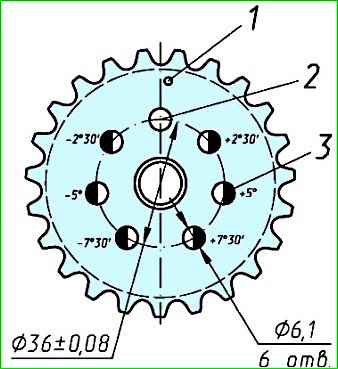
5. Using the jig installed on the sprocket, in each sprocket, drill six additional holes 3 (Figure 7) Ø 6.1 mm with angular displacements of 2°30', 5°00' and 7°30' from the nominal position of the factory hole 2, located along the axis of symmetry one of the cavities of the sprocket teeth.
At the same time, three additional holes, offset from the axis of symmetry of the tooth cavity clockwise, are positive, three others, offset counterclockwise, are negative, if you look at the sprocket from the side of mark 1.
If, when adjusting the valve timing, it is necessary to rotate the camshaft(s) in the direction of its rotation (clockwise), then the sprocket(s) must be installed on one of the additional holes with a positive offset, located to the right of the factory hole, if - counterclockwise, then install the sprocket (s) on one of the holes with a minus offset, located to the left of the factory hole.
The selection of a hole on the sprocket with the required displacement value is made depending on the deviation of the angular position of the cam from the nominal value.
When installing the sprocket on the additional hole, the factory alignment mark 1 on the sprocket will not coincide with the top plane of the cylinder head.
Example
As an example, consider the adjustment of valve timing when the template arrow readings are 23°30′ for the intake valve cam and 16°30′ for the exhaust valve cam, these angle values exceed the nominal values for the intake and exhaust cams by 3°, which is more than permissible deviation ±2°40'.
With these readings of the angular position of the cams and taking into account that when the engine is running, the camshafts rotate clockwise, observing from the side of the crankshaft pulley, the beginning of the opening of the intake and exhaust valves will occur with some advance from the factory values of the valve timing.</ p>
To adjust the phases, in this case, it is necessary to turn the camshafts counterclockwise and when installing the sprockets, use an additional hole with a minus angular offset, with an offset value of 2°30' (the first hole located to the left of the factory hole).
Continue the work in the following sequence:
- 1. Turn with a 27 mm wrench and install the exhaust camshaft so that the arrow on the template was opposite the protractor mark 19°30’.
- 2. Throw the chain over the sprocket and orient its first accessory hole, located to the left of the factory hole, so that it is in front of the camshaft pin, and the drive branch of the chain (in the area of the middle guide) is tensioned.
To install the sprocket on the camshaft flange and pin, slightly turn the camshaft clockwise using the square wrench.
After installing the sprocket, turn the camshaft counterclockwise to tighten the drive branch of the chain, while the arrow of the template installed on the cam should show 19°30’±2°40’.
- 3. Install the intake camshaft so that the template arrow is opposite the protractor mark 20°30’.
- 4. Install the sprocket on the intake camshaft in the same way as the exhaust camshaft sprocket, using the same additional hole.
In this case, with the leading branch of the chain tensioned (in the area of the upper damper), the arrow of the template installed on the cam should show 20˚30′±2˚40′.
- 5. Pre-tighten the sprocket mounting bolts (key “12”).
- 6. Disassemble and assemble (“charge”) the hydraulic tensioner, install it in the hole in the cylinder head, close the lid, tighten the lid bolts, and unscrew the plug from the lid.
- 7. Using a metal rod or a screwdriver, press the hydraulic tensioner through the hole in the hydraulic tensioner cover, moving it all the way, then release it - the hydraulic tensioner will “discharge” when the locking ring on the plunger disengages with the hydraulic tensioner body and allows the plunger and housing to move under the action of the spring.< /li>
The body will move all the way to the lid, and the chain will be tensioned through the tensioner lever.
- 8. Screw the plug into the hydraulic tensioner cover, having previously applied Stopper - 6 sealant to the threads of the plug.
- 9. Check the correct setting of the valve timing by turning the crankshaft two turns in the direction of rotation and aligning the marks on the damper pulley and the chain cover.
Check using a protractor and a cam template as described above. The arrow of the template installed on the intake cam should show 20°30’±2°40’, and on the exhaust cam 19°30’±2°40’.
If this condition is not met, it is necessary to repeat the installation of the valve timing.
- 10. Screw in and tighten the bolts securing the camshaft sprockets to a final torque of 56-62 Nm (5.6 - 6.2 kgf m).
- 11. Install the upper and middle chain guides by screwing in and tightening the fastening screws to a torque of 20-25 Nm (2.0 - 2.5 kgf m) (wrench “6” for bolts with a hex socket, torque wrench with head “6”).
Preliminarily apply Stopor-6 sealant to the screws securing the dampers.
- 12. Reassemble the engine in the reverse order of disassembly
After adjusting the valve timing, the engine should run like clockwork.