Zu den Hauptmängeln des Zylinderkopfes, die durch eine Reparatur behoben werden können, gehören: Verformung der Kontaktebene mit dem Zylinderblock, Verschleiß von Sitzen und Ventilführungen
Die Nichtgeradheit der Ebene des Kopfes in Kontakt mit dem Block sollte bei der Überprüfung auf der Kontrollplatte mit einer Fühlerlehre nicht mehr als 0,05 mm betragen.
Geringe Verformungen des Kopfes (bis zu 0,3 mm) sollten durch Abkratzen der Oberfläche am Lack beseitigt werden. Bei einem Verzug über 0,3 mm muss der Kopf geschliffen werden.
Ventildichtheit wiederherstellen und Ventilbuchsen austauschen
Eine Verletzung der Ventildichtheit bei korrektem Spiel zwischen Ventilschäften und Kipphebeln sowie bei ordnungsgemäßem Betrieb des Vergasers und der Zündanlage wird durch charakteristische Knallgeräusche vom Schalldämpfer und Vergaser erkannt.
Der Motor läuft unregelmäßig und entwickelt nicht die volle Leistung.
Stellen Sie die Dichtheit der Ventile wieder her, indem Sie die Arbeitsfasen der Ventile an ihren Sitzen schleifen.
Wenn sich an den Arbeitsfasen von Ventilen und Sitzen Hohlräume, Ringnuten oder Kratzer befinden, die nicht durch Läppen entfernt werden können, schleifen Sie die Fasen und schleifen Sie dann die Ventile an die Sitze.
Ventile mit verzogenen Köpfen ersetzen.
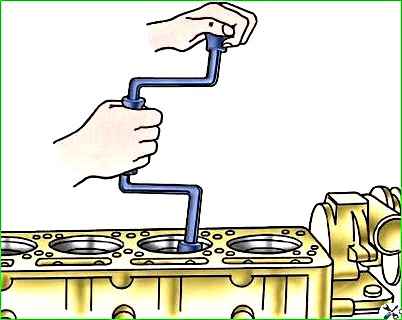
Die Ventilfasen mit einer pneumatischen oder elektrischen Bohrmaschine Modell 2213, 2447 GARO oder manuell mit einer Klammer schleifen.
Führen Sie das Schleifen mit hin- und hergehenden Drehbewegungen durch, bei denen sich das Ventil in die eine Richtung etwas mehr dreht als in die andere.
Für die Zeit des Einschleifens eine Auslösefeder mit leichter Elastizität unter dem Ventil einbauen.
Der Innendurchmesser der Feder sollte etwa 10 mm betragen.
Die Feder sollte das Ventil leicht über den Sitz heben und bei leichtem Druck sollte das Ventil auf dem Sitz sitzen.
Das Werkzeug wird über einen Gummisaugnapf mit dem Ventil verbunden, wie in Abb. 2.
Für eine bessere Haftung des Saugnapfes am Ventil müssen deren Oberflächen trocken und sauber sein.
Um das Läppen zu beschleunigen, verwenden Sie eine Läpppaste, die aus einem Teil M20-Mikropulver und zwei Teilen Motoröl besteht.
Vor Gebrauch gründlich mischen.
Beginnen Sie mit dem Schleifen, bis auf den Arbeitsflächen von Sitz und Ventilteller entlang des gesamten Umfangs eine gleichmäßige matte Fase entsteht.
Reduzieren Sie gegen Ende des Läppens den Gehalt an Mikropulver in der Läpppaste.
Beenden Sie das Einschleifen mit einem sauberen Öl. Anstelle der Läpppaste können Sie auch 00-Schmirgelpulver gemischt mit Motoröl verwenden.
Zum Schleifen der Arbeitsfasen von Ventilen wird die Verwendung von Schleifmaschinen vom Typ R-108 oder OPR-1841 GARO empfohlen.
Gleichzeitig spannen Sie die Ventilstange in die Zentrierpatrone des Spindelstocks ein, die in einem Winkel von 44°30' zur Arbeitsfläche des Schleifsteins angebracht ist.
Die Reduzierung des Neigungswinkels der Arbeitsfase des Ventilkopfes um 30' im Vergleich zum Fasenwinkel der Sitze beschleunigt das Einfahren und verbessert die Dichtheit der Ventile.
Entfernen Sie beim Schleifen eine minimale Menge Metall von der Ventilkopffase.
Die Höhe des zylindrischen Gürtels der Arbeitsfase des Ventilkopfes muss nach dem Schleifen mindestens 0,7 mm betragen und die Koaxialität der Arbeitsfase relativ zur Stange muss innerhalb von 0,03 mm der Gesamtanzeigewerte liegen.
Der Ventilschaftschlag beträgt nicht mehr als 0,02 mm. Ersetzen Sie Ventile mit großem Schlag durch neue.
Schleifen Sie die Ventilschäfte nicht auf eine kleinere Größe nach, da dies die Herstellung neuer Ventilfederhalter erfordern würde.
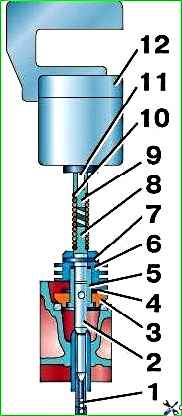
Schleifen Sie die Fasen der Sitze in einem Winkel von 45° koaxial zum Loch in der Buchse. Die Fasenbreite sollte 1,6–2,4 mm betragen.
Zum Schleifen von Sitzen empfiehlt sich die Verwendung des in Abb. gezeigten Geräts. 2.
Schleifen Sie den Sitz ohne Läpppaste oder Öl, bis der Stein die gesamte Arbeitsfläche erreicht.
Nach der groben Bearbeitung tauschen Sie den Stein gegen einen feinkörnigen aus und schleifen den Sattel fertig.
Der Fasenschlag relativ zur Achse des Ventilhülsenlochs sollte 0,03 mm nicht überschreiten.
Ersetzen Sie abgenutzte Sitze durch neue.
Ventilsitze, deren Außendurchmesser um 0,25 mm größer als der Nenndurchmesser ist, werden als Ersatzteile geliefert.
Entfernen Sie abgenutzte Sitze mit einem Senker vom Kopf.
Nach dem Entfernen des Sed Die Buchsen im Kopf für das Auslassventil auf einen Durchmesser von 38,75+0,025 mm und für das Einlassventil auf einen Durchmesser von 49,25+0,25 mm aufgebohrt.
Bevor Sie die Sitze verpressen, erhitzen Sie den Zylinderkopf auf eine Temperatur von 170 °C und kühlen Sie die Sitze mit Trockeneis ab.
Drücken Sie schnell, ohne dass sich die Sitze erwärmen. Der gekühlte Kopf bedeckt die Sättel dicht.
Um die Festigkeit der Sitze zu erhöhen, verstemmen Sie sie mit einem flachen Dorn entlang des Außendurchmessers und stellen Sie sicher, dass die Sitzfase ausgefüllt ist.
Dann auf die erforderlichen Maße schleifen und überrunden.
Wenn der Verschleiß des Ventilschafts und der Führungsbuchse so groß ist, dass der Spalt in ihrer Verbindung 0,25 mm überschreitet, stellen Sie die Dichtheit des Ventils erst wieder her, nachdem Sie das Ventil und seine Buchse ausgetauscht haben.
Ersatzteile werden mit Ventilen nur in Nenngrößen und Führungsbuchsen mit einem um 0,3 mm reduzierten Innendurchmesser zum anschließenden Reiben auf die endgültige Größe nach dem Einpressen in den Zylinderkopf geliefert.
Verlängern Sie die gepressten Buchsen auf einen Durchmesser von 9+0,022 mm.
Der Einlassventilschaft hat einen Durchmesser von 9 – 0,050 – 0,075 mm, das Auslassventil hat einen Durchmesser von 9 – 0,075 – 0,095 mm, daher sollten die Abstände zwischen den Einlass- und Auslassventilschäften und Buchsen 0,050 – 0,097 betragen mm bzw. 0,075–0,117 mm.
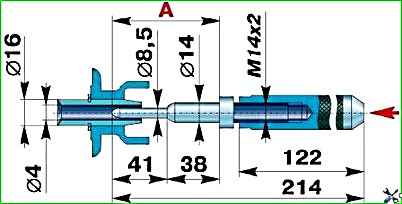
Verschlissene Führungsbuchsen mit dem in Abb. gezeigten Dorn aus dem Zylinderkopf drücken. 3.
Drücken Sie die neue Buchse von der Kipphebelseite her mit demselben Dorn bis zum Anschlag in den Haltering an der Buchse.
Erhitzen Sie in diesem Fall wie beim Pressen von Ventilsitzen den Zylinderkopf auf eine Temperatur von 170 °C und kühlen Sie die Hülse mit Trockeneis.
Nachdem Sie die Ventilbuchsen ausgetauscht haben, schleifen Sie die Sitze (mittig auf den Löchern in den Buchsen) und schleifen Sie dann die Ventile daran an.
Nach dem Schleifen der Sitze und der Ventile gründlich ausspülen und alle Kanäle und Stellen, an denen Schleifmittel eindringen könnte, mit Druckluft ausblasen.
Ventilbuchsen bestehen aus Metallkeramik und sind porös.
Nach dem Fertigstellen und Waschen tränken Sie sie mit Öl. Führen Sie dazu mehrere Stunden lang einen mit Spindelöl getränkten Filzdocht in jede Buchse ein.
Vor dem Zusammenbau schmieren Sie die Ventilschäfte mit einer dünnen Schicht einer Mischung aus sieben Teilen eines kolloidalen Graphitölpräparats und drei Teilen Motoröl.
Ventilfedern austauschen
Mögliche Fehlfunktionen der Ventilfedern, die während des Betriebs auftreten, können sein: verminderte Elastizität, Brüche oder Risse in den Spulen.
Überprüfen Sie die Elastizität der Ventilfedern, wenn Sie den Ventilmechanismus zerlegen.
Die Kraft, die erforderlich ist, um eine neue Ventilfeder auf 46 mm Höhe zusammenzudrücken, sollte 267–310 N (27,3–31,7 kgf) und bis zu 37 mm 686–784 N (70–80 kgf) betragen.
Wenn die Druckkraft einer Feder mit einer Höhe von bis zu 46 mm weniger als 235 N (24 kgf) und bis zu einer Höhe von 37 mm weniger als 558,6 N (57 kgf) beträgt, ersetzen Sie eine solche Feder durch eine neue .
Ersetzen Sie Federn mit Brüchen, Rissen und Korrosionsspuren durch neue.
Drücker austauschen
Die Führungslöcher im Block für die Drücker verschleißen leicht. Stellen Sie daher das Nennspiel in diesem Zusammenhang wieder her, indem Sie die verschlissenen Drücker austauschen.
Als Ersatzteile werden nur Drücker mit Nenngröße geliefert.
Wählen Sie Drücker für Löcher mit einem Spalt von 0,040–0,015 mm.
Drücker werden je nach Größe des Außendurchmessers in zwei Gruppen eingeteilt und mit einem Stempel gekennzeichnet: Nummer 1 – für einen Drückerdurchmesser von 25 – 0,008 – 0,015 mm und Nummer 2 – für einen Drückerdurchmesser von 25 -0,015 -0,022 mm.
Ein richtig ausgewählter Drücker, geschmiert mit flüssigem Mineralöl, sollte sich unter seinem Eigengewicht sanft in die Blockaufnahme absenken und sich darin leicht drehen lassen.
Drücker, die radiale Abnutzung an den Enden der Platten aufweisen, abgenutzt sind oder an der Arbeitsfläche abplatzen, ersetzen Sie sie durch neue.
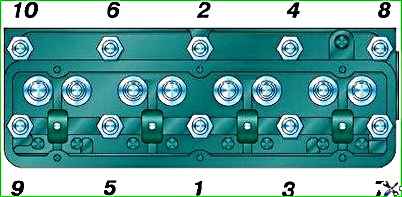
Zylinderkopfmuttern nach dem Einfahren des Fahrzeugs, nach 1000 km und nach jedem Kopfausbau festziehen.
Ziehen Sie die Muttern nur bei kaltem Motor in der in Abb. gezeigten Reihenfolge fest. 4 in zwei Schritten.
Endgültiges Anzugsdrehmoment 71,5–76,5 Nm (7,3–7,8 kgf·m).
Reinigen Sie bei Bedarf den Zylinderkopf, die Kolbenböden und die Einlassventile von Kohlenstoffablagerungen.
An einem funktionstüchtigen, ungetragenen Motor, unter Verwendung von hochwertigem Kraftstoff und Öl und unter Beobachtung Wenn die richtigen thermischen Bedingungen aufrechterhalten werden, sind die Ablagerungen gering.
Wenn der Motor, insbesondere seine Kolbenringe, verschleißt, gelangt viel Öl in die Brennräume und es bildet sich eine große Schicht Kohlenstoffablagerungen.
Das Vorhandensein von Kohlenstoffablagerungen wird durch erhöhte Detonation, Überhitzung, Leistungsverlust und erhöhten Kraftstoffverbrauch festgestellt.
Wenn diese Anzeichen auftreten, entfernen Sie den Zylinderkopf und entfernen Sie Kohlenstoffablagerungen mit Metallschabern und Bürsten.
Achten Sie darauf, dass keine Kohlenstoffablagerungen in den Spalt zwischen Kolbenköpfen und Zylindern gelangen.
Wenn der Motor mit bleihaltigem Benzin betrieben wurde, befeuchten Sie die Kohlenstoffablagerungen zunächst mit Kerosin, um zu verhindern, dass Sie beim Reinigen giftigen Staub einatmen.