Zylinderkopf demontieren und zusammenbauen
Entfernen Sie den Zylinderkopf nur zur Fehlerbehebung bei Teilen der Zylinder-Kolben-Gruppe, der Zylinderkopfdichtung, den Ventilen oder um den Kopf selbst auszutauschen
Entfernen Sie den Zylinderkopf in der folgenden Reihenfolge:
- 1. Lassen Sie das Kühlmittel aus dem Motorkühlsystem ab
- 2. Trennen Sie alle Rohrleitungen vom Kopf und schützen Sie ihre inneren Hohlräume vor Staub und Schmutz
- 3. Zylinderkopfhaube abnehmen
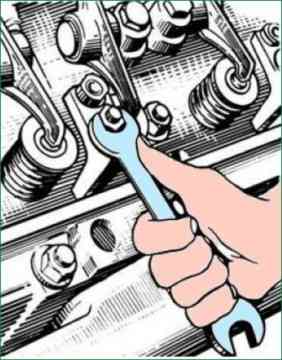
Schrauben Sie die Muttern der Düsenhalterungen ab (Abb. 1), entfernen Sie die Düsen (Abb. 2) und schützen Sie so den Zerstäuber vor Stößen und Verstopfungen der Löcher.
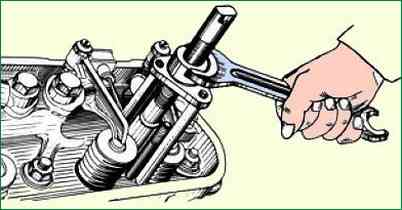
Lösen Sie die Muttern, mit denen die Kipphebelachsen befestigt sind, entfernen Sie die Kipphebelachsenbaugruppe mit den Kipphebeln und entfernen Sie die Stangen.
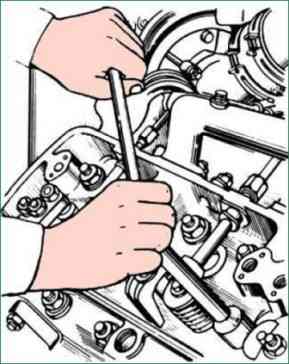
Lösen Sie die Zylinderkopfmuttern (Abb. 3) und befolgen Sie dabei die umgekehrte Reihenfolge wie beim Anziehen (Abb. 4) in mindestens drei Schritten:
- - I - Empfang - bis zu 147-118 Nm (15-12 kgf m)
- - II - Empfang - bis zu 49-39 Nm (5-4 kgf m)
- - III- Trick – Schrauben Sie die Muttern ab.
- 7. Nehmen Sie den Zylinderkopf vom Motor ab und überprüfen Sie seinen Zustand.
- 8. Entfernen Sie bei Bedarf vorsichtig die Zylinderkopfdichtung.
- 9. Überprüfen Sie den Zustand der Zylinderlaufbuchsen und verschließen Sie die Zylinderbohrungen, um sie vor Staub und Schmutz zu schützen.
Montieren Sie den Zylinderkopf in umgekehrter Reihenfolge am Motor.
Wischen Sie vor dem Einbau die Passflächen des Zylinderblocks, der Schulter der Zylinderlaufbuchse und des Zylinderkopfs mit einem sauberen Lappen ab.
Die Wiederverwendung der metallischen Zylinderkopfdichtung mit demselben Zylinderkopf ist nur zulässig, wenn die Position der Laufbuchsen im Zylinderblock unverändert bleibt und keine Anzeichen eines Gasdurchbruchs im Gasverbindungsbereich vorliegen.
Eine Wiederverwendung von Gummidichtungen und -dichtungen ist nur möglich, wenn keine Risse, Beschädigungen oder Verhärtungen vorliegen.
Achten Sie auf den korrekten Einbau der Gummidichtung und Dichtungen.
Die Gewinde müssen mit sauberem Motoröl geschmiert werden.
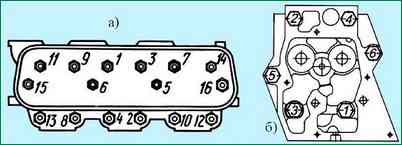
Ziehen Sie die Zylinderkopfmuttern bei kaltem Motor in aufsteigender Reihenfolge der Zahlen an, wie in Abb. 4 in mindestens drei Schritten:
- - I - Empfang - 39-49 Nm (4-5 kgf m);
- - II – Empfang – 118–147 Nm (12–15 kgf m);
- - III - Empfang - 216-235 Nm (22-24 kgf m).
Prüfen Sie nach dem Anziehen mit einem zweiten Vorgang das erforderliche Drehmoment an jeder Mutter und befolgen Sie dabei die angegebene Reihenfolge.
Ziehen Sie die Muttern niemals mit einem höheren Drehmoment als angegeben an, da dies unweigerlich zur Zerstörung von Teilen führt und die Dichtheit der Dichtung nicht verbessert wird.
Läppen von Ventilen
Bevor Sie die Zylinderköpfe zerlegen, reinigen Sie sie von Öl- und Kohlenstoffablagerungen und markieren Sie die Seriennummern der Ventile an den Enden der Platten, um sie bei der Montage an ihren Plätzen zu installieren.
Um die Ventile zu trocknen, ist es notwendig, den Zylinderkopf ohne Einspritzdüsen, Kipphebel, Kipphebelachsen und Kipphebelachs-Befestigungsbolzen mit der Passfläche auf der Platte zu installieren, um einen Anschlag für die Ventile zu bieten.
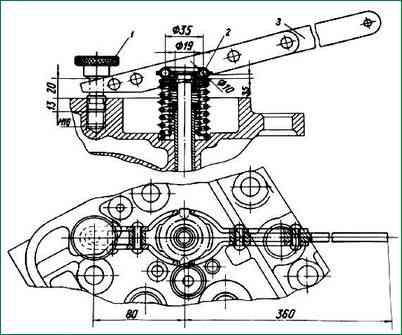
Die Trocknung erfolgt mit dem in Abb. dargestellten Gerät. 5.
Zu diesem Zweck schrauben Sie den Anschlagbolzen 1 des Geräts in das Loch für den Bolzen zur Befestigung der Kipphebelachse, montieren die Druckplatte 2 des Geräts auf dem Federteller des entsprechenden Ventils und drücken den Griff 3 des Gerätehebels, drücken Sie die Ventilfedern, entfernen Sie die Cracker und entfernen Sie alle Teile der Ventilbaugruppe.
Auf die gleiche Weise alles nacheinander trocknen andere Ventile und entfernen Sie die Ventilfedern und zugehörigen Teile.
Drehen Sie den Zylinderkopf und entfernen Sie die Ventile aus den Führungen. Reinigen Sie die Ventile und Sitze gründlich von Schmutz, Kohlenstoffablagerungen und Ölablagerungen, spülen Sie sie mit Kerosin oder einer speziellen Reinigungslösung ab, trocknen Sie sie und überprüfen Sie den Reparaturgrad.
Es ist nur möglich, die Dichtheit des Ventils durch Läppen wiederherzustellen, wenn leichte Abnutzung und kleine Löcher an der Arbeitsfase vorhanden sind, und nur wenn die Platte und der Schaft nicht verzogen sind und keine lokalen Ausbrennungen an den Fasen des Ventils vorhanden sind Ventil und Sitz.
Bei Vorliegen solcher Mängel sollte dem Läppen das Schleifen von Sitzen und Ventilen oder der Austausch defekter Teile vorausgehen.
Verwenden Sie zum Läppen der Ventile eine spezielle Läpppaste, die durch gründliches Mischen von drei Volumenteilen grünem Siliziumkarbid-Mikropulver mit zwei Teilen Motoröl und einem Teil Dieselkraftstoff hergestellt wird.
Rühren Sie die Läppmischung vor der Verwendung gründlich um, da ohne mechanisches Rühren das Mikropulver ausfallen kann.
Montieren Sie den Zylinderkopf mit der Passfläche nach oben auf einer Platte oder einem Spezialwerkzeug.
Tragen Sie eine dünne, gleichmäßige Schicht Läpppaste auf die Ventilfläche auf, schmieren Sie den Ventilschaft mit sauberem Motoröl und bauen Sie ihn in den Zylinderkopf ein.
Es ist erlaubt, die Paste auf die Fase des Sattels aufzutragen.
Das Läppen erfolgt durch hin- und hergehende Drehbewegungen der Ventile mit einem Spezialwerkzeug oder einer Bohrmaschine mit Absaugung.
Drücken Sie das Ventil mit einer Kraft von 20–30 N (2–3 kgf), drehen Sie es um eine ⅓ Umdrehung in eine Richtung und drehen Sie es dann, indem Sie die Kraft lockern, um eine viertel Umdrehung in die entgegengesetzte Richtung.
Mappen Sie nicht in kreisenden Bewegungen.
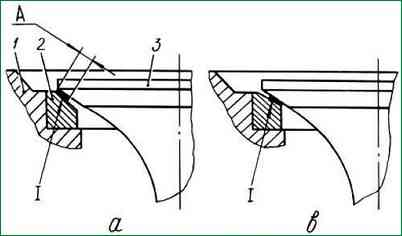
Heben Sie das Ventil regelmäßig an und geben Sie Paste auf die Fase. Fahren Sie mit dem Läppen fort, wie oben angegeben, bis ein durchgehendes mattes Band mit einer Breite "A" von mindestens 1,5 mm auf den Fasen des Ventils und des Sitzes erscheint (Abb. 6). ).
Risse des Mattenbandes und das Vorhandensein von Querspuren darauf sind nicht zulässig.
Bei ordnungsgemäßer Läppung sollte das matte "A"-Band auf der Ventilsitzschräge an der größeren Basis des Kegels beginnen, wie in Abbildung 6 dargestellt.
Nach dem Läppen die Ventile und den Zylinderkopf gründlich mit Kerosin oder einer speziellen Reinigungslösung waschen und trocknen.
Achtung! Schon geringe Rückstände der Läpppaste am Ventil oder Zylinderkopf können zu Riefenbildung und beschleunigtem Verschleiß der Zylinderlaufbuchsen und Kolbenringe führen.
Montieren Sie die Ventile, Federn und deren Befestigungsteile am Zylinderkopf und trocknen Sie die Ventile mit dem Werkzeug (siehe Abb. 5).
Überprüfen Sie die Schleifqualität der Ventil-Sitz-Schnittstelle auf Undichtigkeiten, indem Sie Kerosin oder Dieselkraftstoff abwechselnd in die Einlass- und Auslasskanäle einfüllen.
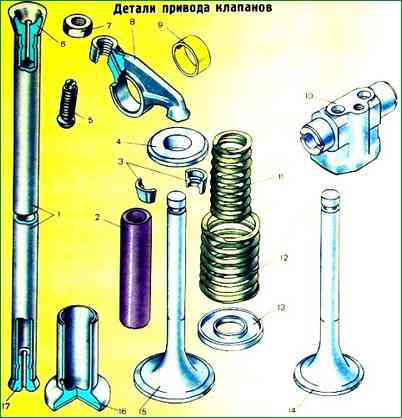
Gut geschliffene Ventile sollten eine Minute lang kein Kerosin oder Diesel durchlassen.
Die Qualität des Läppens kann mit einem Bleistift überprüft werden.
Tragen Sie dazu in regelmäßigen Abständen 10–15 Striche mit einem weichen Graphitstift auf die Fase des geläppten, sauberen Ventils auf, setzen Sie das Ventil dann vorsichtig in den Sitz ein und drehen Sie es unter kräftigem Druck gegen den Sitz um eine Vierteldrehung.
Wenn die Läppqualität gut ist, sollten alle Striche auf der Arbeitsfase des Ventils gelöscht werden.
Sollten die Ergebnisse der Läppqualitätsprüfung nicht zufriedenstellend sein, muss diese fortgesetzt werden.