Wir führen Reparaturen am Zylinderkopf bei allgemeinen Motorreparaturen und beim Austausch der Zylinderkopfdichtung durch
Es ist sehr wichtig, den Kopf zu reparieren, nachdem der Motor überhitzt ist.
Bei Überhitzung können Mängel auftreten, die optisch möglicherweise nicht sichtbar sind
Daher müssen Sie alle Arbeiten zur Reparatur des Zylinderkopfs sorgfältig durchführen.
Der Betrieb des Motors hängt maßgeblich davon ab. Und das erspart Ihnen unnötigen Aufwand und Kosten.
Wir betrachten den Ausbau des Zylinderkopfes im Artikel – Zylinderkopfdichtung ZMZ 405 GAZ-2705
Zylinderkopf demontieren
Muttern 1 abschrauben und Schirm 5 des Phasensensors, Halterung 2 zum Anheben des Motors und Abgaskrümmer 6 entfernen.
Entfernen Sie die Auspuffkrümmerdichtungen.
Schrauben Sie die Schraube 3 ab und entfernen Sie den 4. Phasensensor.
Schrauben Sie den Notöldrucksensor 7 und die Öldruckanzeige 8 ab.
Lösen Sie Klemme 1 und entfernen Sie den Schlauch vom Leerlaufluftreglerrohr.
Muttern 2 abschrauben und Empfänger 3 vom Zulaufrohr abnehmen.
Entfernen Sie die Empfängerdichtung.
Muttern 1 abschrauben und Ansaugrohr 2 samt Einspritzdüsen und Kraftstoffleitung abnehmen (auf dem Foto nicht dargestellt).
Entfernen Sie die Ansaugrohrdichtung.
Schrauben Sie die Schrauben 1 ab und entfernen Sie die hintere Abdeckung 2 des Blockkopfes.
Entfernen Sie die Deckeldichtung
Hydraulikstößel 1 ausbauen. Es ist bequemer, hydraulische Drücker mit einem Magneten oder Saugnapf zu entfernen
Hydraulische Drücker können nicht ausgetauscht werden, daher müssen sie vor dem Ausbau markiert werden, damit sie bei der Montage an ihrem Platz eingebaut werden können.
Hydraulikheber sollten in der gleichen Position wie auf den Ventilen gelagert werden, damit kein Öl aus ihnen austritt.
Wenn die Konstruktion des Abziehers keinen Ventilanschlag vorsieht, platzieren Sie einen geeigneten Anschlag darunter.
Komprimieren Sie die Federn mit einem Trockenmittel.
Um das Entfernen der Federplatte aus den Crackern zu erleichtern, können Sie mit einem Hammer einen leichten Schlag auf das hartnäckige Zweibein des Trockenmittels ausüben.
Entfernen Sie zwei Cracker mit einer Pinzette und lösen Sie die Federn sanft.
Entfernen Sie die obere Platte und zwei Ventilfedern.
Entfernen Sie den Öldeckel mit einem Abzieher...
Entfernen Sie mit einem Schraubendreher die Stützscheibe 1 der Ventilfedern.
Umdrehen Entfernen Sie den Zylinderblock und entfernen Sie das Ventil. Markieren Sie dabei den Einbauort, damit das Ventil bei der anschließenden Montage an seinen ursprünglichen Platz zurückkehrt. Ebenso entfernen und markieren wir die restlichen Ventile.
Verschlissene Ventilführungen pressen wir mit einem Dorn aus
Verwenden Sie einen „8“-Inbusschlüssel, um die Ölkanalstopfen abzuschrauben
Inspektion, Fehlerbehebung und Reparatur des Zylinderkopfes
Nach dem Zerlegen des Zylinderkopfes alle Teile in Benzin waschen, abwischen und trocknen. Reinigen Sie Brennräume und Ventile von Kohlenstoffablagerungen.
Inspizieren Sie den Blockkopf.
Bei Rissen an den Stegen zwischen den Ventilsitzen, Brandflecken und Rissen an den Wänden des Brennraums den Zylinderkopf austauschen.
Überprüfen Sie mit einem Metalllineal und Fühlerlehren, ob die Ebenheit der Oberfläche des Kopfes neben dem Block gebrochen ist.
Legen Sie dazu das Lineal mit der Kante mittig, längs und dann quer auf die Oberfläche des Blockkopfes und messen Sie mit einer Fühlerlehre den Abstand zwischen der Oberfläche des Kopfes und dem Lineal. Wenn der Spalt mehr als 0,1 mm beträgt, tauschen Sie den Kopf aus.
Überprüfen Sie das Spiel in den Nockenwellenlagern.
Überprüfen Sie die Abstände zwischen den hydraulischen Ventilstößeln und den Kanälen für die hydraulischen Stößel im Zylinderkopf.
Der Spalt wird als Differenz zwischen dem Durchmesser des Kanals und dem Durchmesser des hydraulischen Schiebers berechnet.
Der Nenndurchmesser des Kanals für den hydraulischen Schieber beträgt 35,0 +0,025 mm, der maximal zulässige Durchmesser beträgt 35,1 mm.
Der Nenndurchmesser des hydraulischen Stößels beträgt 35,0 - 0,025 und 35,0 - 0,041 mm, der maximal zulässige Durchmesser beträgt 34,95 mm. Der maximal zulässige Spalt beträgt 0,15 mm.
Wenn der Spalt den angegebenen Wert überschreitet, ersetzen Sie den Hydrostößel. Wenn dies kein positives Ergebnis liefert, tauschen Sie den Blockkopf aus.
Inspizieren Sie die Ventile.
Wenn auf der Arbeitsfläche des Ventils Risse, eine Verformung des Ventilkopfes, ein Durchbrennen oder eine Verformung des Schafts festgestellt werden, muss das Ventil ausgetauscht werden.
Kleinere Flecken und Kratzer auf der Arbeitsfläche des Ventils können durch Läppen entfernt werden.
Das Ventil wird wie folgt in den Sitz eingeschliffen:
- - Setzen Sie das Ventil in den Blockkopf ein;
- - Setzen Sie eine Ventilschleifvorrichtung auf den Ventilschaft;
- - Tragen Sie eine dünne Schicht Läpppaste, eine Mischung aus feinem Schleifpulver und Motoröl, auf die Arbeitsfase des Ventils auf;
- - Drehen Sie das Ventil mit der Vorrichtung in beide Richtungen und drücken Sie es dabei regelmäßig gegen den Sitz.
Ein äußeres Zeichen für ein zufriedenstellendes Läppen ist die gleichmäßige mattgraue Farbe der Arbeitsfase von Sitz und Ventil.
Wischen Sie nach dem Läppen den Sitz und das Ventil mit einem sauberen Tuch ab und spülen Sie es gründlich aus, um die restliche Läpppaste zu entfernen.
Um die Dichtheit des Ventils zu überprüfen, installieren Sie es zusammen mit Federn und Splinten im Blockkopf.
Danach legen Sie den Blockkopf auf die Seite und gießen Kerosin in den durch das Ventil verschlossenen Kanal. Wenn innerhalb von 3 Min. Kerosin gelangt nicht in die Brennkammer, das Ventil gilt als abgedichtet.
Überprüfen Sie den Zustand der Ventilfedern. Verbogene, gerissene oder gebrochene Federn müssen ersetzt werden.
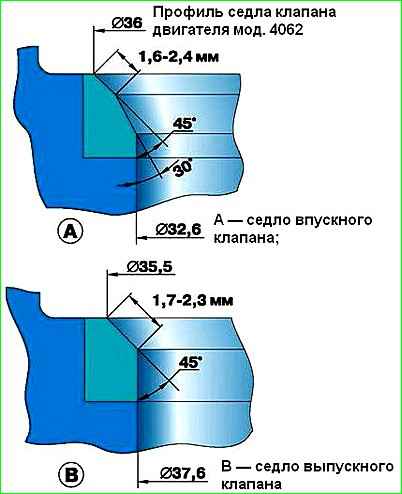
Überprüfen Sie den Zustand der Ventilsitze. Die Arbeitsfasen der Sitze dürfen keine Anzeichen von Abnutzung, Löchern, Korrosion usw. aufweisen.
Kleinere Beschädigungen (kleine Flecken, Kratzer etc.) können durch Einschleifen der Ventile entfernt werden.
Größere Mängel können durch Schleifen beseitigt werden. Halten Sie beim Schleifen die in der Abbildung angegebenen Sitzmaße ein
Überprüfen Sie nach dem Schleifen den Rundlauf der Sitzfase im Verhältnis zum Loch in der Ventilführung. Der maximal zulässige Rundlauf beträgt 0,05 mm.
Nach dem Schleifen die Ventile schleifen.
Anschließend den Zylinderkopf gründlich reinigen und mit Druckluft ausblasen, damit keine abrasiven Partikel in den durch die Ventile verschlossenen Kanälen und in den Brennräumen zurückbleiben.
Es ist zu beachten, dass das Ventil nach dem Schleifen des Sitzes tiefer im Sitz sitzt.
Deshalb müssen Sie nach dem Schleifen den Abstand zwischen dem Ende des gegen den Sitz gedrückten Ventilschafts und der Nockenwellenachse messen.
Wenn dieser Abstand weniger als 35,5 mm beträgt, ersetzen Sie den Zylinderkopf, da in diesem Fall die normale Funktion der Ventilstößel gestört ist.
Überprüfen Sie die Abstände zwischen den Führungsbuchsen und Ventilen.
Der Spalt wird als Differenz zwischen dem Durchmesser des Lochs in der Buchse berechnet und Ventilschaftdurchmesser. Der maximal zulässige Spalt beträgt 0,2 mm.
Wenn der Spalt den angegebenen Wert überschreitet, ersetzen Sie das Ventil und die Führungshülse.
Die alte Buchse wird mit einem Dorn seitlich aus der Brennkammer herausgedrückt.
Neue Buchsen mit aufgesetzten Sicherungsringen einbauen, bis der Sicherungsring in der Ebene des Blockkopfes auf der Seite des Lochs für die hydraulischen Drücker stoppt.
Vor dem Einbau müssen die Buchsen auf –40...45°C abgekühlt und der Blockkopf auf eine Temperatur von +160-175°C erwärmt werden.
Die Buchse sollte frei oder mit wenig Kraftaufwand in den Blockkopf eingeführt werden.
Ventilführungen werden als Ersatzteile in drei Reparaturgrößen geliefert.
Die erste Reparaturgröße mit einem um 0,02 mm vergrößerten Außendurchmesser der Buchse.
Der zweite ist der Außendurchmesser der Hülse 14,2 +0,053 und 14,2 +0,040 mm, der dritte ist mit einem um 0,02 mm vergrößerten Durchmesser gegenüber der zweiten Größe.
Beim Einbau von Buchsen der ersten Reparaturgröße das Loch für die Buchse nicht in den Blockkopf bohren.
Beim Einbau von Buchsen der zweiten und dritten Reparaturgröße müssen Sie das Loch auf einen Durchmesser von 14,2 - 0,023 und 14,2 - 0,050 mm bohren.
Erweitern Sie nach dem Einbau der neuen Buchsen das Loch für die Ventile darin auf die in der Tabelle angegebenen Abmessungen. 2.1. Anschließend die Ventilsitze wie oben beschrieben schleifen.
Um den Blockkopf auf Risse zu prüfen, müssen Sie einen Druckluftschlauch an eines der Löcher im Kühlmantel anschließen.
Verschließen Sie alle Löcher im Kopf mit Holzstopfen. Senken Sie den Kopf in ein Wasserbad und wenden Sie Druckluft mit einem Druck von 1,5 atm an. An Stellen mit Rissen können Luftblasen austreten.
Nachdem wir die Passebene des Kopfes gereinigt haben, überprüfen wir die Qualität der Passung des Kopfes am Block mit einer geraden Kante.
Wenn die Verformung mehr als 0,05 mm beträgt, muss die Ebenheit durch mechanische Behandlung wiederhergestellt werden. Wenn die Nichtebenheit jedoch 0,1 mm überschreitet, wird der Kopf nicht repariert.
Verwenden Sie Kerosin oder Dieselkraftstoff, um den Kopf zu spülen und die Ölkanäle von Ablagerungen zu befreien.
Anschließend wischen wir die Oberflächen mit einem sauberen Lappen ab und blasen die Kanäle mit Druckluft aus. Ersetzen Sie die Ölkanalstopfen
Wir pressen neue Ventilbuchsen durch einen Aluminium-Abstandshalter, erwärmen den Kopf auf 160–180 °C und kühlen die Buchsen in „Trockeneis“ (CO 2).
Bauen Sie die Ventile in umgekehrter Reihenfolge wie beim Ausbau ein und ersetzen Sie dabei die alten Öldichtungen durch neue
Läppen der Ventile
Tragen Sie Läpppaste auf die Ventilfase auf und installieren Sie sie in der entsprechenden Kopfbuchse.
Befestigen Sie eine Läppvorrichtung am Ventilschaft und drücken Sie das Ventil gegen den Sitz und drehen Sie es in beide Richtungen um ca. 90°
Wir schleifen weiter, bis die Ventildichtfase über die gesamte Breite und Länge matt und sauber ist.
Die Fase am Ventilsitz sollte auch so aussehen. Wischen Sie restliche Paste mit einem Lappen vom Ventil und Sitz ab.
Zylinderkopf in umgekehrter Reihenfolge zusammenbauen.